In the power distribution system, Power cables are the main material used to transport electricity. Currently, The most common electrical cables are those with a copper core and those made of aluminum alloy. Does 40 years, cable industry developed AA8000 series aluminum alloy as conductive material. Currently, more than 90% of municipal projects, civilians, Industrial and commercial in the United States use AAAC cables (aluminum alloy conductors).
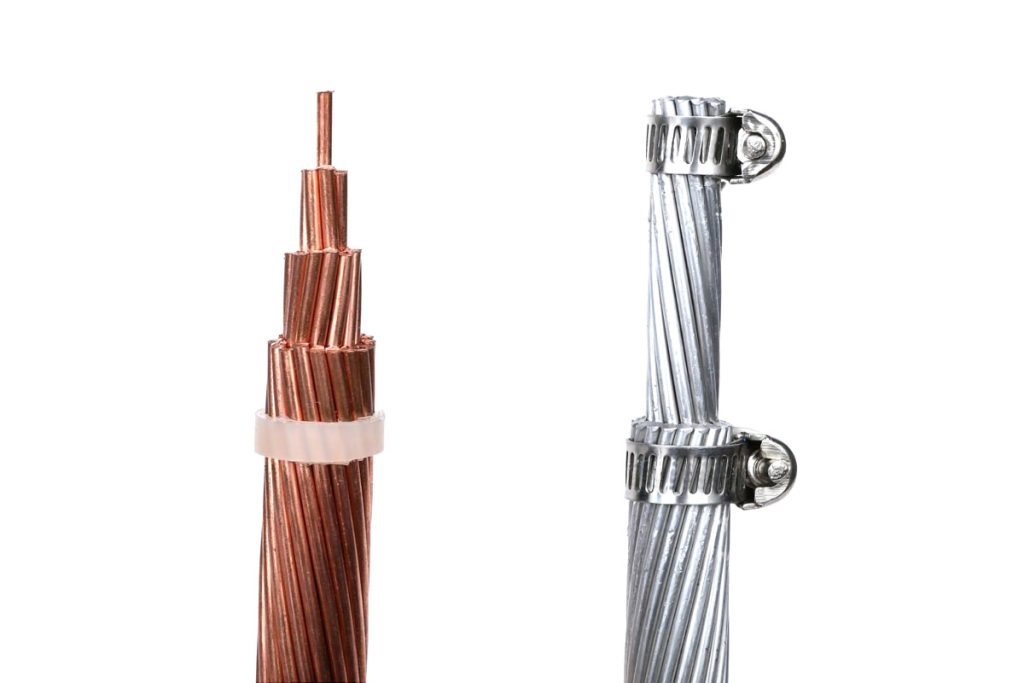
Table of Contents
AAAC cables incorporate alloying elements such as copper, hierro, magnesium, silicon, zinc and boron in electrical aluminum. Using special manufacturing processes, such as braiding and annealing treatment, a is produced new type of cable. Depending on the composition of the alloy, Aluminum alloy cables are mainly divided into two categories: alloy wires represented by AA8030 and rare earth aluminum alloy wires represented by AA8176. Both categories are commonly known as AA8000 aluminum alloy cable series.
So, What are the differences between AAAC cables and copper cables? Next, we will carry out a comparative analysis in terms of technical parameters, installation and construction, total costs and operational maintenance.
Technical Parameters
Technical parameters are important indicators in the selection of materials for equipment. Here, we compare AA8030 aluminum alloy conductor with copper conductor. In the technical parameters, It is crucial to pay attention to the cable's current capacity and voltage losses.
Performance comparison between alloy cables and copper cables
Features | Density (g/mm3) | Resistivity (Ωxmm2/m) | Conductivity (IACS%) | Tensile strength (MPa) | Elastic limit (Mpa) | Elongation (%) |
---|---|---|---|---|---|---|
electrical copper | 8.89 | 0.017241 | 100 | 220-270 | 60-80 | 30-45 |
Aluminium alloy | 2.7 | 0.0279 | 61.8 | 113.8 | 53.9 | 30 |
According to the previous table, the density of aluminum alloy is only one third of that of electrical copper, its resistivity is 1.6 times that of copper and its conductivity is 61.8% of copper. The tensile strength of aluminum alloy is about half that of copper, and its resistance to creep and elongation are close to the lower limit of copper. We focus especially on the comparison of conductivity and resistivity, since the technical parameters directly related to conductivity are current capacity and resistivity is directly related to voltage losses. Next, A comparative analysis of these two parameters is carried out.
Comparison condition: The cross section of the aluminum alloy cable is 1.5 times that of copper wire.
Comparison of cross section and current capacity between copper wires and aluminum alloy wires
Material | Cable section (mm2) | cable outer diameter (mm) | Bridge laying capacity(A) | Pipe laying capacity(A) |
---|---|---|---|---|
Copper | 16 | 22.3 | 100 | 79 |
Aluminium alloy | 25 | 25.2 | 97 | 78 |
Copper | 25 | 27.6 | 127 | 101 |
Aluminium alloy | 35 | 28.4 | 120 | 94 |
Copper | 35 | 30.6 | 158 | 122 |
Aluminium alloy | 50 | 31.4 | 146 | 112 |
Copper | 50 | 32.7 | 192 | 144 |
Aluminium alloy | 70 | 35.6 | 187 | 138 |
Copper | 70 | 38 | 246 | 178 |
Aluminium alloy | 120 | 41.2 | 263 | 186 |
Copper | 95 | 41.3 | 298 | 211 |
Aluminium alloy | 150 | 47.5 | 304 | 210 |
Copper | 120 | 46.4 | 346 | 240 |
Aluminium alloy | 185 | 51.9 | 347 | 236 |
Copper | 150 | 50.5 | 399 | 271 |
Aluminium alloy | 240 | 56.4 | 409 | 272 |
Copper | 185 | 55.3 | 456 | 304 |
Aluminium alloy | 300 | 62.4 | 478 | 308 |
Comparison of cross section and voltage losses between copper cables and aluminum alloy cables
Material | Cable section (mm2) | Endurance (Ω/km α=80°C) | Voltage loss(%(Akhkm) cosφ=0.8) |
---|---|---|---|
Copper | 16 | 1.359 | 0.518 |
Aluminium alloy | 25 | 1.348 | 0.512 |
Copper | 25 | 0.870 | 0.340 |
Aluminium alloy | 35 | 0.869 | 0.339 |
Copper | 35 | 0.622 | 0.249 |
Aluminium alloy | 50 | 0.617 | 0.248 |
Copper | 50 | 0.435 | 0.180 |
Aluminium alloy | 70 | 0.430 | 0.178 |
Copper | 70 | 0.310 | 0.134 |
Aluminium alloy | 120 | 0.308 | 0.120 |
Copper | 95 | 0.229 | 0.105 |
Aluminium alloy | 150 | 0.224 | 0.101 |
Copper | 120 | 0.181 | 0.087 |
Aluminium alloy | 185 | 0.179 | 0.080 |
Copper | 150 | 0.145 | 0.074 |
Aluminium alloy | 240 | 0.140 | 0.071 |
Copper | 185 | 0.118 | 0.064 |
Aluminium alloy | 300 | 0.112 | 0.059 |
According to the above information, when the cross section of the aluminum alloy wire is 1.5 times that of electrical copper cable, The current capacity and voltage losses of both cables are practically the same under similar temperature conditions.
Installation and Construction
During the installation and construction process, It is crucial to pay attention to the mechanical properties of aluminum and copper alloy conductors, which include the following aspects.
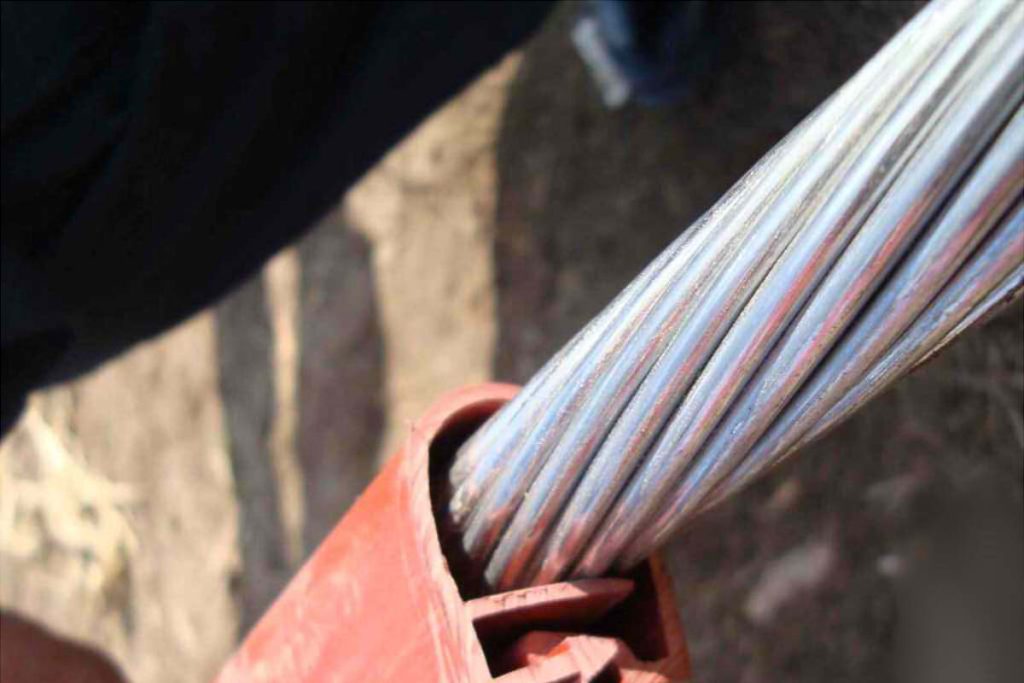
Flexibility
The bending radius of the aluminum alloy conductor cable is 7 times the diameter of the cable, while that of the copper conductor cable is 10 a 20 times the diameter. Aluminum alloy cable is easier to bend during installation, which effectively reduces installation costs and reduces the risk of accidents.
Elasticity
The elasticity of aluminum alloy conductor it's a 40% less than that of copper. If both cables, aluminum and copper alloy, are bent 90° and stress is released under the same temperature conditions, the rebound angle of the aluminum alloy cable is only the 60% of the copper cable. The use of AAAC cables significantly reduces the elastic stress caused by the conductor during installation, facilitating construction.
Flexibility
The flexibility of the aluminum alloy conductor is a 25% greater than that of copper. It has superior plasticity, high fatigue resistance and is easy to process and shape. Can be bent repeatedly without developing cracks or breaking, which improves the safety of wiring lines.
Extension Rate
Extension rate is a key indicator of cable quality and resistance to external forces. After annealing treatment, The extension rate of the aluminum alloy conductor cable can increase up to 30%, while that of the copper conductor cable is 25%. This indicates that aluminum alloy cables are more flexible than conventional copper cables, meaning less pulling force is required during installation.
In summary, during the installation and construction process, The mechanical properties of aluminum alloy conductors exceed those of copper cables.
Total Costs
Acquisition Costs
In general, to achieve the same electrical performance, direct acquisition costs of aluminum alloy cables (including specialized connection terminals and racks) are approximately a 20% – 40% lower than copper cables. Because unarmored aluminum alloy cables require an increase in cable cross section to achieve the same electrical performance, this results in an increase in the cross section of the frames. This increases the costs of the main material of the racks, but the total acquisition costs when using aluminum alloy cables are reduced.
Installation Costs
According to the cable laying method, The auxiliary materials needed for cable installation also vary. When installing copper cables indoors as main cables, rack laying is generally used. According to regulatory requirements, The cross section of cables laid on racks should not be higher than the 40% of frame cross section. Nevertheless, Shielded aluminum alloy cables do not require the use of racks.
Taking as an example a project budget of $20 million for the acquisition of cables: if aluminum alloy cables are used, can save approximately $1.8 million in installation costs, which represents a saving of 50% compared to installation costs of copper cables. This savings in installation costs represents the 8% of the total budget of cable acquisition.
Operation and maintenance
during operation, it is necessary to pay attention to several characteristics of the cables, like energy loss, resistance to plastic flow, corrosion resistance, fire resistance and service life.
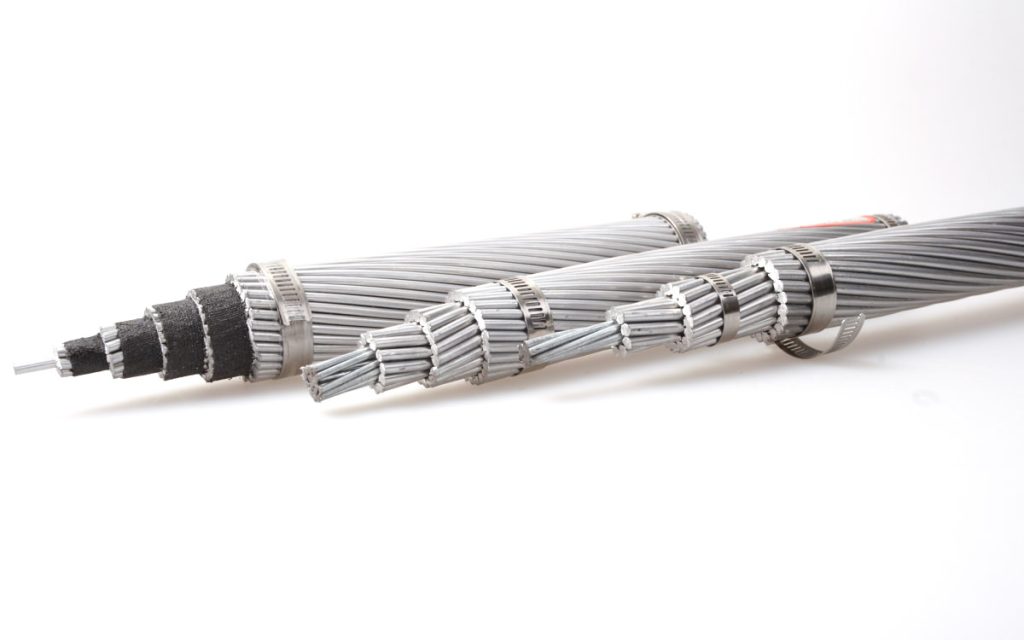
Energy Loss
According to the formula for calculating losses in cable lines, at equal operating currents, Losses in lines of AAAC expanded cables and copper cables are practically the same.
Resistance to Plastic Flow
The phenomenon in which strain increases with time under constant stress is called creep. Cables are subject to constant tensions during installation and long-term connection. If the resistance to plastic flow is low, connections can loosen over time, increasing contact resistance and creating a risk to the safe operation of the line. Aluminum alloy wires allow the alloying elements to dissolve in the aluminum matrix, forming a solid solution. This makes it difficult for the solute atoms to deform by sliding., significantly improving resistance to plastic flow. Therefore, Aluminum alloy cables can achieve plastic flow resistance similar to that of copper cables.
Corrosion Resistance
Aluminum's unique corrosion resistance comes from the oxide layer that naturally forms on its surface when it comes into contact with air.. This oxide layer can resist various types of corrosion. Alkaline soils and some types of acidic soils have a high corrosive potential for aluminum, so AAAC bare cables should not be buried directly and should be protected with a cover to prevent corrosion. Nevertheless, in environments with the presence of sulfur, like railway tunnels, The corrosion resistance of aluminum exceeds that of copper.
Fire resistance
The insulation of armored aluminum alloy cables uses XLPE material (cross-linked polyethylene) low smoke and halogen free. Besides, Its unique self-adjusting shielding structure contributes to a low-smoke, halogen-free fire rating (IA). Self-adjusting shielding improves the heat dissipation capacity and fire resistance properties of the cable. Nevertheless, because the melting point of aluminum is 660°C, Aluminum alloy cables should not be used in emergency power supply lines requiring continuous supply during fires. Nevertheless, for other supply circuits requiring low smoke emission and halogen-free fire resistance, self-adjusting aluminum alloy cables can be used.
Lifespan
Under favorable operating conditions, The lifespan of copper cables is usually around 30 years, while the service life of aluminum alloy cables can reach 40 years.
Conclusion
In summary, AAAC cables are essentially equivalent to copper cables in terms of technical parameters and power loss., being superior in other aspects when used as bare conductors in overhead lines. It is expected that in the future, with continuous improvement in research into conductive materials and manufacturing technologies, The application of aluminum alloy cables will attract more and more attention from the industry.