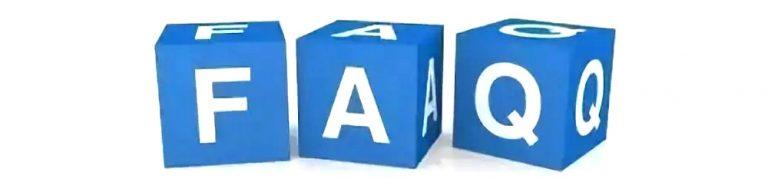
ZMS helps you solve problems you may encounter when selecting power cable products.. Contact us if you have any questions or would like more detailed advice on your selection needs. We offer you the solutions for cables that suit your needs.
Selection of Electrical Cable and Fiber Optic

To select a suitable cable, the first step is to calculate the theoretical current for normal operation according to the power of the load.
For a normal single phase circuit: Current = Charge / operating voltage
Once the current, You can use the electrical cable specification table to select the cable with the appropriate cross section.
In general, each square millimeter of cross-section of the copper wire can pass a current of approximately 4,5 a 5 A.
The copper is more conductive than aluminum. Usually, The resistivity of aluminum conductors is approximately 1,68 times greater than that of copper conductors. Therefore, a copper wire is about a 30% higher than the permissible load capacity of an aluminum cable with the same cross section.
Since copper conductors are approximately 3,5 times more expensive than aluminum, and copper is heavier than aluminum, aluminum cables are commonly used for most overhead lines.
Due to weight requirements, overhead cables typically use aluminum conductors or braided steel and aluminum cables. Instead, underground cables typically use copper conductors, who are more drivers.
Underground cables are prone to accidents if they leak, so they need thick insulation. Besides, to avoid damage by external forces, underground cables are usually armored.
Aerial cables are mostly bare conductors because air is a natural insulating medium and there is less risk of electric shock..
DC wires (direct current cables) used in rectified direct current transmission systems. Compared to AC cords, DC cables have less power loss during transmission and are easy to install and maintain. They are also less expensive.
AC cords (alternating current cables) are commonly used in power frequency power systems. AC cables have high safety requirements on insulation. They are more complex in construction and cost about three times as much as DC cables..
More information: The Difference Between DC Cable and AC Cable
For circuits with voltage levels of 1 kV and below, can be selected from 1 a 5 cable cores based on different grounding safety requirements.
For three-phase power circuits medium and high voltage, can be selected 3 single-conductor cables per circuit when operating current is high or when laying underwater. In addition to the above, cables should be used 3 cores.
For high voltage AC single-phase power circuits, as in the electrified railways, cables should be used 2 cores the 2 single conductor cables per circuit.
For DC high voltage transmission systems, single conductor cables must be used.
Los most common insulation materials for the cables are PVC, PE, XLPE, goma, etc.
Among them, PVC material has the advantages of simple structure, easy fabrication and processing, light weight and lower cost. Therefore, It is widely used in insulation for medium and low voltage cables..
XLPE cables have higher overload capacity and longer lifespan compared to PVC. But they are also more expensive than PVC. PVC cables typically have a life expectancy of 20 years in good surroundings. While, XLPE cables typically have a life expectancy of 40 years.
Rubber cables are soft and flexible. They have a small radius of curvature. This type of cables is suitable for use in scenarios where frequent movement is required, like sea cables, mining cables, etc.
Allowable long-term operating temperature: 70°C (PVC), 90°C (XLPE/ERP)
Maximum allowable temperature in case of short circuit: 160°C (PVC), 250°C (XLPE/ERP)
If the current passing through a conductor of electricity is high, a magnetic field is generated around the current. So as not to affect other components, it is necessary to add a shielding layer to shield this electromagnetic field inside the conductors. This also protects them from the influence of external electromagnetic fields..
The shielding cables it is made mainly of non-magnetic materials, like copper and aluminum. It is usually woven copper mesh or copper tape. Multi-conductor cables are usually shielded to isolate electromagnetic interference between the conductors.
Usually, medium and high voltage cables 6 kV and higher have a shield for the conductor and a shield for the insulation. Some low voltage cables are not shielded. Instrument wires and cables must be shielded.
The shielding protective layer can be added to any cable structure to increase mechanical strength, tensile strength, compressive strength, etc. It also protects cables from external damage and prolongs their lifespan..
In general, underground cables must use armored cables. Armored cables are also often required in environmentally demanding usage scenarios, like the chemical industry, metallurgy, machinery construction and underwater power transmission.
Cables often have different structures and properties depending on the different needs of different application scenarios.. The choice of cable can be divided according to the scope of the industry, for example, construction engineering cables, mining cables, railway cables, communication cables, airport cables, solar cables, etc.
For high-rise buildings, the underground passages, large power plants and industrial and mining applications with fire safety requirements, fire resistant cables or flame retardant cables should be used. For places with environmental requirements, environmentally friendly cables should be used, like the LSZH cable (low smoke zero halogen cable).
Flame retardant cables have self-extinguishing properties and are difficult to burn. They can prevent the fire from spreading, preserving other equipment and preventing further damage.
Fire-resistant cables are cables that can be kept in operation for a certain period of time in the event of a fire.. They are often used in emergency power circuits to ensure the normal operation of circuits in the event of a fire..
Fire resistant cables are much safer. Usually, fire resistant cables can replace flame retardant cables, but flame retardant cables cannot replace fire resistant cables.
long transmission distance: Fiber optic connections can be up to 70 km.
Fast transmission speeds: Fiber optic access is capable of providing high-speed bandwidth, like 100Mbps and 200Mbps.
low loss: Fiber optic medium is manufactured to extremely high purity, so fiber loss is extremely low. Therefore, it can reduce the number of relay stations in the communication line and greatly improve the quality of communication.
High resistance to interference: As plastic optical fiber is a non-metallic material, is immune to electromagnetic interference
More information: The Difference Between Indoor and Outdoor Fiber Optic Cables
Indoor fiber optic cables have lower tensile strength and are more brittle. Nevertheless, they are also lighter and cheaper. This type of optical fiber is mainly used for the internal wiring of buildings and for the interconnection of network equipment..
Las outdoor fiber optics have an additional layer of metallic armor than those for interiors. Aerial optical fibers have a higher tensile strength and are mainly used for interconnection between buildings and remote networks..
ADSS fiber optic cable has no metal in its structure, so it is resistant to electromagnetic interference and lightning. Can be built using existing towers, which saves line construction costs. The fibra ADSS can be used in strong electrical environments, like railways, in lightning-prone areas and in complex terrain over long distances.
OPGW fiber optic cable construction is metal clad fiber optic units. The OPGW cable can be laid at the base of overhead high voltage transmission lines (110kV, 220kV, 500kV, etc.) to form a fiber optic communication network. The OPGW fiber It has both ground and communication functions and can effectively improve the utilization rate of towers.
The number of cores of the fiber optic cable is mainly related to the application system. Determining the number of fiber cores depends on how many fiber cores are used in the specific application, plus the number of redundant cores on the line.
The number of fiber cores is not related to the number of data points, but only with the number of fiber nodes.
Usually, for FTTH lines they are used 1 a 2 fiber cores. For the operation and integration of the system are used 4 a 48 fiber cores. And fiber optic trunk cables usually have 48 cores or more.
Multimode fiber supports hundreds of transmission modes. This type of fiber has the advantage of high bandwidth and low cost.. It is suitable for transmission over short distances (less than 2000 metros).
Singlemode fiber can only transmit one mode of signal wave. Since the optical signal in single-mode fibers only travels in a straight line, the transmission bandwidth is very wide. Therefore, single-mode fibers are suitable for backbone communications systems, high capacity and long distance.
Singlemode fibers use a laser diode as a light source.. So, its price is slightly higher.
Currently, single-mode fibers are used more, while multimode fibers are being phased out.
Submarine fiber optic cables have to be protected against seawater corrosion, withstand underwater pressure and prevent being damaged by external forces. Therefore, the structure of submarine optical fibers is very complex.
The internal fibers must be wrapped with high tensile steel wires., filling all gaps with waterproof material during the wrapping process. A layer of copper tape wraps around the steel wires to form a combination of compressive and tensile strength.. Another layer of polyethylene coating is required on the outside of the copper tape.
This complex multi-layer structure is designed to ensure stable operation of the undersea fiber optic internet.
