Failures in electrical circuits are currently the main “cause” of the fires, and its causes include: the use of non-fireproof electrical cables, damage to electrical cable conductors, faults in electrical cable connections, cable insulation aging, among others, that cause fires. Therefore, to prevent fires, The choice of materials for electrical cables is especially important. Currently, the cable industry pays great attention to a new type of fire-resistant cable: ceramizable silicone cable.
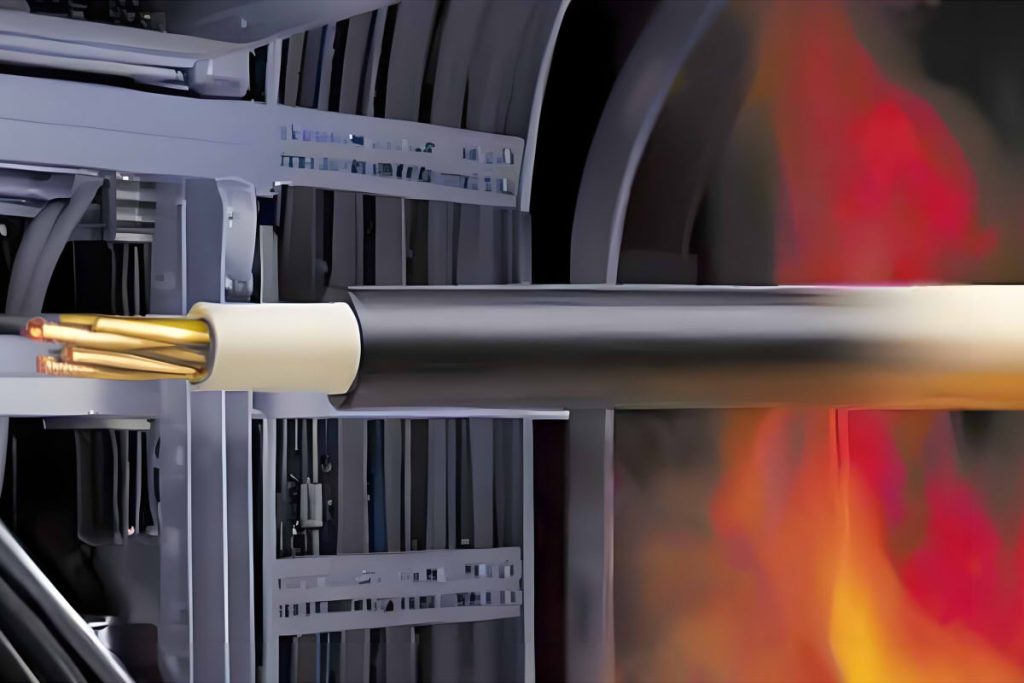
Table of Contents
- New materials drive the development of fire-resistant cables
- Characteristics of ceramizable silicone
- Ceramizable Silicone Fire Resistant Cables
New materials drive the development of fire-resistant cables
Currently, The most commonly used fire resistant insulation cables are MI fire insulation cables Magnesium oxide mineral and fire resistant cables wrapped in mica tape. Although both have good properties of resistance to high temperatures and combustion, mineral magnesium oxide cable is difficult to install due to its installation complexity and high raw material cost, making it difficult to use on a large scale.
Secondly, mica tape wrapped fire resistant cable requires multiple layers of wrapping during the production process. Due to limitations in manufacturing conditions, It is common for defects to occur in the joints, and after being burned, mica tape becomes brittle and tends to come off, which affects the fire resistance effect.
With the advancement in research on fire-resistant insulation cables, a high-performance temperature-resistant elastomer has emerged: ceramizable silicone. This fire resistant silicone combines the flexibility and elasticity of silicone and, when exposed to temperatures above 500 °C and flame erosion, turns into a hard ceramic-like substance, blocking the spread of fire. The longer the exposure time and temperature, firmer it becomes, with a heat resistance that can reach up to 1200-1500 °C, protecting objects exposed to fire from damage.
The use of ceramizable silicone as insulation in electrical cables allows, when exposed to fire, form a rigid protective layer that protects the conductor, becoming the key research and application focus in the fire resistant cables industry.
Comparison of fire resistant cables
Parameter | Fire Resistant Magnesium Oxide Cable | Fire resistant cable wrapped in mica tape | Fire-resistant ceramizable silicone cable |
---|---|---|---|
Advantages | 1) High overload protection capacity; 2) Good resistance to corrosion and explosion. | 1) Excellent resistance to high temperatures and combustion; 2) Does not emit toxic fumes when burned. | 1) Good strength and high resistance to thermal shock; 2) Halogen free, low smoke emission, low toxicity, self-extinguishing and ecological; 3) Easy to process. |
Fire resistance effect | Bueno | Bueno | Bueno |
Isolation effect | Disabled; insulation is susceptible to chemical reactions with humidity in the air. | Disabled; detachment of mica tape reduces the insulation effect. | Bueno; forms a rigid ceramic layer that maintains the insulation effect without alterations. |
Installation intensity | Alta | Alta | Baja |
Common installation problems | 1) Insulation resistance may not meet the requirements; 2) Possible short circuits during operation tests; 3) Loss of aesthetics when redoing the work. | 1) It is susceptible to defects in the mica tape joints, that can be detached, affecting fire resistance. | / |
Characteristics of ceramizable silicone
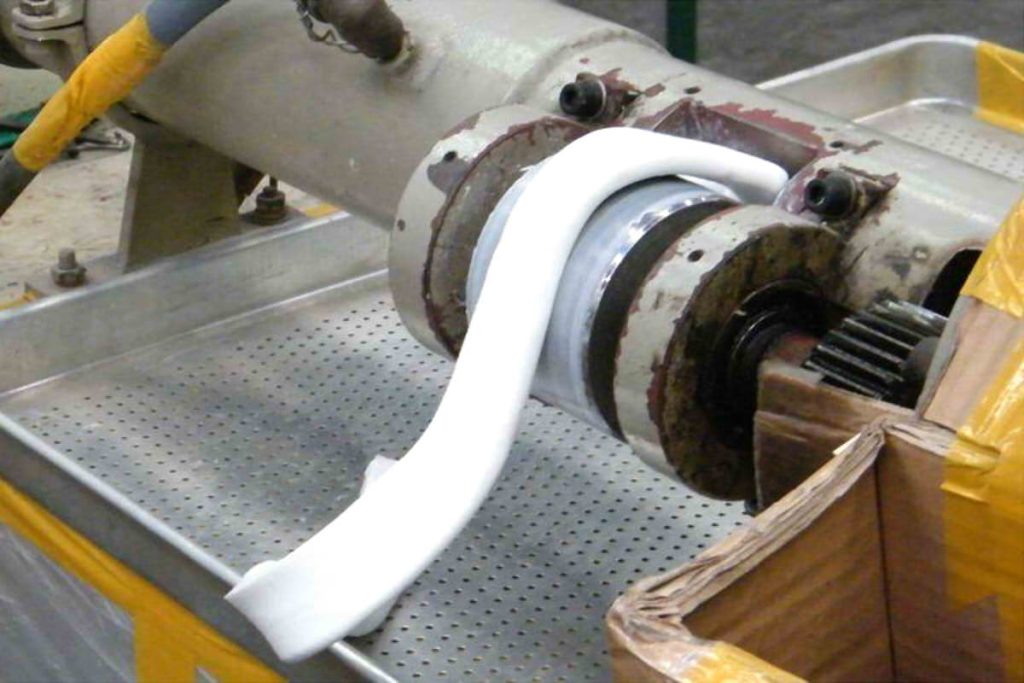
Formation of a self-supporting ceramic body in the presence of flames
When rubber material containing inorganic fillers is exposed to flames, rubber degrades or burns, and the degradation or combustion products volatilize, leaving inorganic residues or ashes with little resistance. These wastes are usually neither coherent nor self-supporting., and even fragment into particles or dust, thus lacking fireproof efficiency. Nevertheless, when ceramizable rubber with a specially designed formula is exposed to flames, depending on the type of rubber and the formula used, can be ceramized between 350 Y 800 °C or more, sinking into a self-supporting and porous ceramic body. At temperatures of 650 a 1000 °C, can maintain its structural integrity for a period of time (0,5 a 2 hours), performing an effective function of “passive fire protection”, providing valuable time for fire safety.
Good resistance, excellent resistance to thermal shock
The sintered ceramizable silicone body it's pretty hard, emitting a ceramic sound when hit, with good resistance to bending and compression. The flexural strength of ceramizable silicone samples is much higher than that of conventional silicone and increases considerably with increasing temperature.. By simulating an extinction process and spraying water on a sample subjected to high temperatures, ceramizable silicone sintered body does not crack, demonstrating excellent resistance to thermal shock.
Halogen free, low smoke emission, low toxicity, self-extinguishing and ecological
Ceramizable silicone does not require halogenated additives to achieve a self-extinguishing flame retardant effect., meeting UL94V flammability classification-0 and with an oxygen index that can reach 38. After a few minutes of exposure to fire, smoke emission completely ceases, and in the subsequent combustion process it does not produce more smoke. Ceramizable silicone is an ecological material that, when burning, produces carbon dioxide, water and silicon dioxide, non-toxic substances.
Good electrical properties
Ceramizable silicone with optimized formula has excellent electrical properties: before sintering, its volumetric resistivity is not less than 10¹⁵ Ω·cm, and although this resistivity decreases as the sintering temperature increases, after 30 minutes of combustion to 1000 °C, its volumetric resistivity remains 10⁷ Ω·cm. The volumetric resistivity of conventional silicone, before and after sintering, nor is it less than 10¹⁵ and 10⁷ Ω·cm, respectively.
Easy to process
The material preparation and production process of ceramizable silicone are similar to those of conventional silicone., and can be processed with standard rubber processing equipment (extruders, vulcanization presses, injection machines, among others). The use of this material simplifies the process of fire resistant cable production, reducing costs.
Ceramizable Silicone Fire Resistant Cables
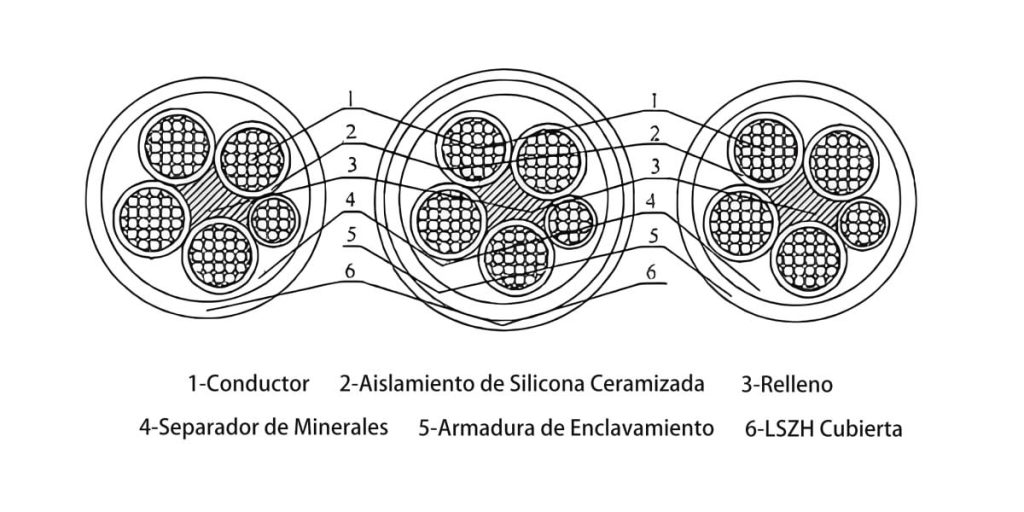
The main application of ceramizable silicone is in fire-resistant medium and low voltage electrical cables., which ensure the safe flow of electricity during a fire. The cable industry shows great interest in the development and application of this new fire-resistant insulation material.
The equipment to produce ceramizable silicone compounds is the same as that used for conventional silicone.. This material has excellent extrusion and molding properties, which allows cables to be manufactured using conventional silicone extrusion and vulcanization equipment without the need to incorporate additional machinery, which significantly reduces production costs.
Besides, ceramizable silicone retains its elasticity at room temperature and, when burning, Does not become brittle or peel off like mica tape, being able to withstand spray and vibration tests. Since in recent years many serious fires in civil buildings have been related to electrical cables, demand for construction cables civil fire resistance is high. Significant future development is anticipated for ceramizable silicone medium and low voltage cables..