When buying cables there are several aspects that must be taken into account. Careful selection will ensure that you purchase cables that are of good quality and meet the requirements of your specific application..
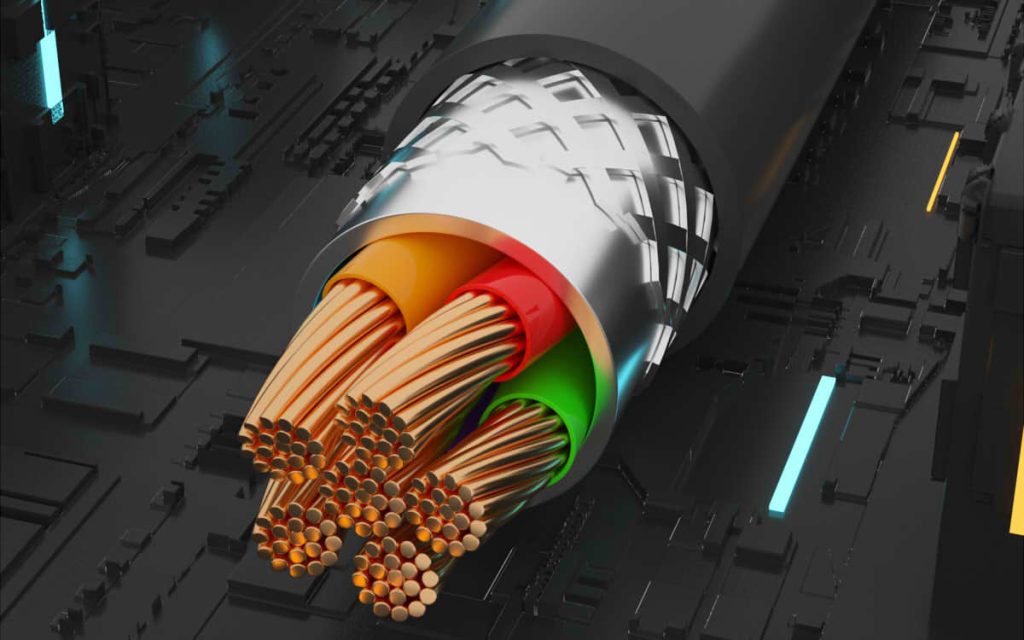
Selection of Materials and Cable Structure
Cable Conductor Selection
Copper, Aluminum and aluminum alloys are the most common conductive materials used in cables. The conductor copper is the recommended option in the following scenarios.
- Critical Circuits, such as power supplies and mobile electronic equipment, where a reliable connection is required.
- Environments with risk of corrosion or explosion for aluminum.
- Applications with high temperatures or fire resistance requirements.
- Nuclear power plants and nuclear energy-related equipment.
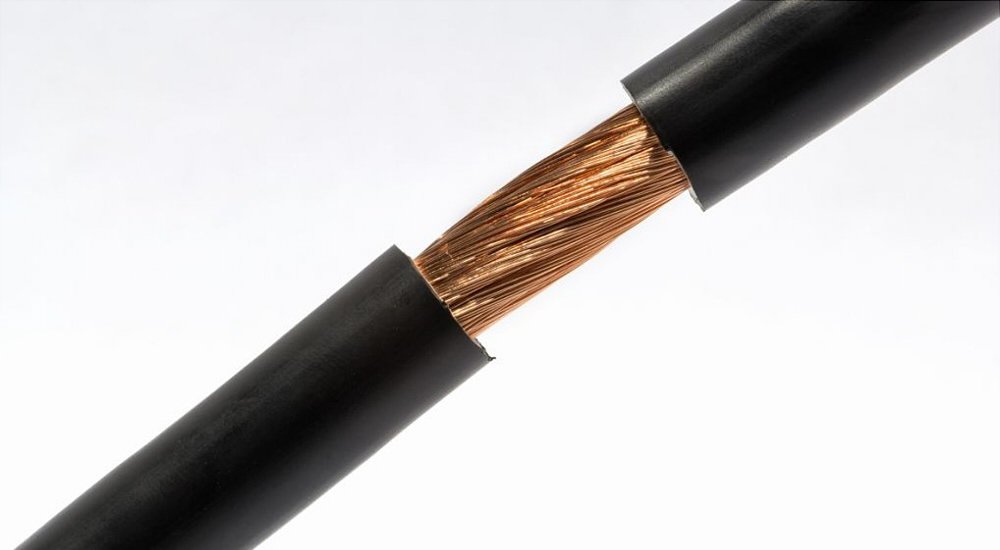
Apart from the above, there are no strict requirements for cable conductors and copper can be chosen, aluminum or aluminum alloy. Aluminum and aluminum alloy conductors are often used in overhead lines due to their lightness and low cost..
Selection of Electrical Cable Insulation
For security reasons, cables must be insulated. Exceptionally, some airlines may use bare conductors. The most commonly used insulation materials are PVC, the XLPE, rubber, mineral insulation, among others.
Selection criteria for PVC insulation
- They can be used on low voltage lines.
- They should not be used in places with high or low temperatures.
- The PVC insulation should not be used in places where environmental protection is required.
- They are not recommended in places with a high influx of people or with low toxicity requirements..
- Heat resistant PVC can be used in places with temperatures above 60°C.
Key factors for XLPE selection
- Can be used for high and low voltage AC.
- The special XLPE can be used for high voltage DC, while the ordinary type is not recommended.
- less than -15℃, cross-linked polyethylene insulation can be used.
- In places with temperatures above 60℃, cable with cross-linked polyethylene insulation can be chosen.
- In places with radiation, radiation-resistant XLPE cables must be used.
- For the circuit of cable submarino de 500kV AC, oil-filled self-capacitating cables or cables with cross-linked polyethylene insulation can be used.
- In crowded places or with low toxicity requirements, cross-linked polyethylene cables and other cables with low-smoke, zero-halogen insulation must be used.
- Nuclear power plants should opt for cross-linked polyethylene cables and other halogen-free insulated cables.
Selection of Rubber Insulation
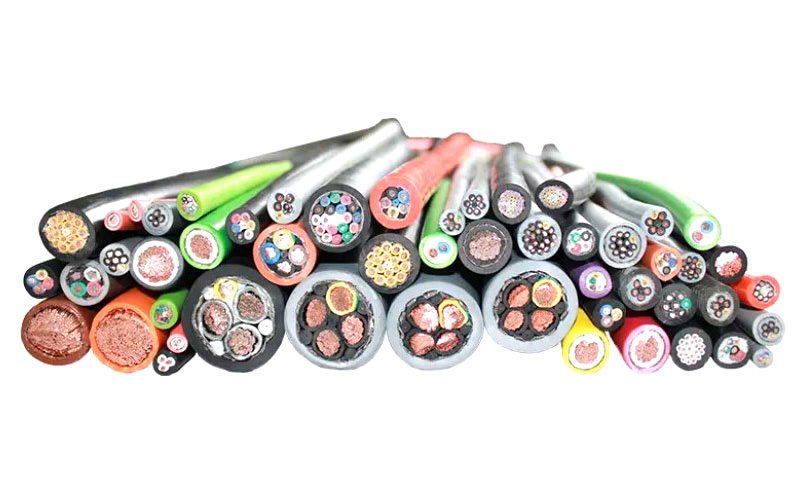
- For circuits that require high flexibility and movement, as mobile electrical equipment, it is recommended to select rubber insulation.
- In environments with temperatures below -15°C, it is better to choose cold-resistant rubber insulation.
- In places with temperatures above 60°C, heat resistant ethylene propylene rubber insulated cables can be used.
- In radioactive environments, it is required to use insulation of ethylene propylene rubber and other materials that are resistant to radiation.
- Nuclear power plants must use cables with ethylene propylene rubber insulation and other materials free of smoke and halogens.
Selection of Mineral Insulation
- Mineral insulated cables are suitable for high temperature environments, higher than 100°C.
- In oil tank areas, Timber-framed important public buildings, high temperature places, and other fire resistance requirements, mineral insulation can be used.
- When fire cables are laid outdoors or when these cables share trenches and wells with other cables, it is necessary to use cables with mineral insulation.
Use of Cable Protection Layers
In environments with high level of electromagnetic noise, It is essential to protect cables against electromagnetic interference by using the shielding such as copper or aluminum tape. If the cable is located in an environment where it is exposed to mechanical damage or erosion, additional layers of protection are required. For example, Underground cables that are directly buried must be armored to improve their resistance to mechanical damage.
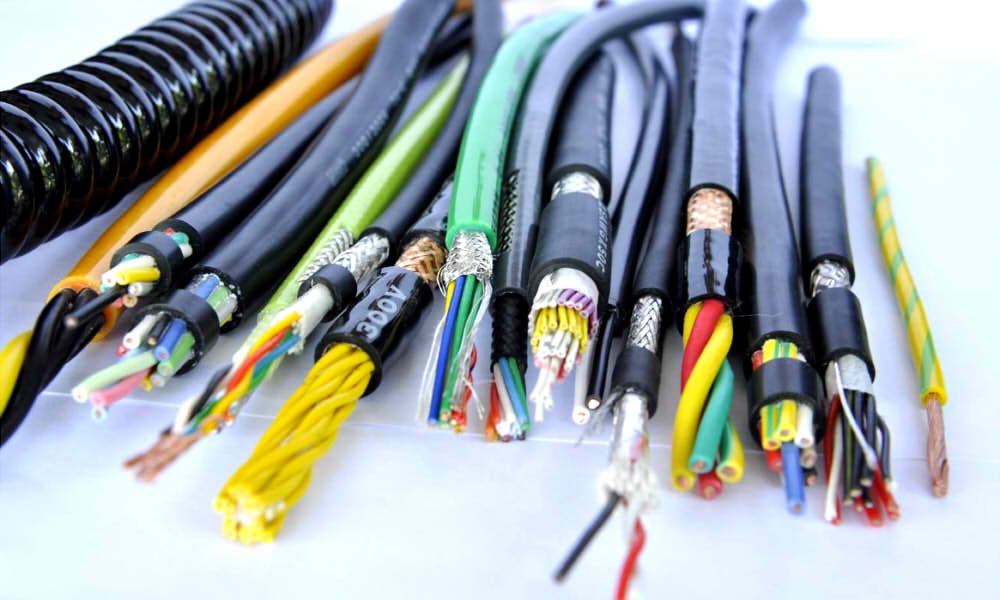
Other Points of the Cable Structure
Besides, when buying cables it is important to consider the number of conductors you have. Most common cables have a variable number of cores, what can they be 1, 2, 3, 4, 5, 3+1, 4+1, 3+2, among others. It is also necessary to know the power rating of the cable, as this determines the necessary cable section. The higher the rated power, the greater the section required.
Distance and Section of Electric Cables
When buying cables, the distance over which the energy will be transported must be taken into account. When cables are supplied over long distances, electrical losses must be taken into account tension fall. To reduce voltage drop, a cable with a larger cross section can be chosen.
Tips for Buying Cables
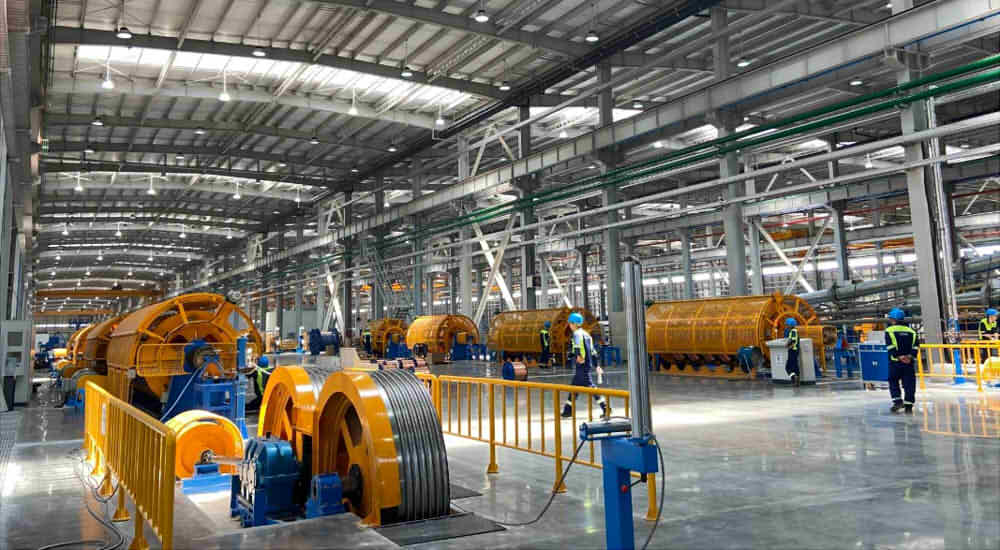
- Check the certification of the cable brand. The mandatory product certification mark must be clearly visible.
- Request a cable inspection report. Cable vendors must be able to provide inspection reports issued by a quality department, since otherwise, the quality of the product would not be guaranteed.
- Check the insulation and jacket of the cable. Insulation and jacket of the cable should have a smooth appearance, without impurities and with a uniform thickness. Besides, They must have some tension and elasticity.
- Analyzes the surface and color of conductors. Copper conductors should be a light purple color and aluminum conductors, of a silvery white color. If the color of the conductor is not correct, it is likely to be contaminated with other materials that reduce its conductivity.
- Check the DC resistance. To guarantee the quality of the cable and wire you purchase, you can do a DC resistance test at an inspection agency, using 3 a 5 meters of the product.
- Choose a formal cable manufacturer. It is important to compare several cable manufacturers before making an informed decision.