Before the XLP revolution (cross-linked polyethylene), Oil-impregnated paper-insulated cables were standard in DC projects. Hoy, Triple layer XLP DC cables have taken the lead due to their economy, Superior energy transport capacity and simplified maintenance, Outperforming traditional cables at all voltage levels.
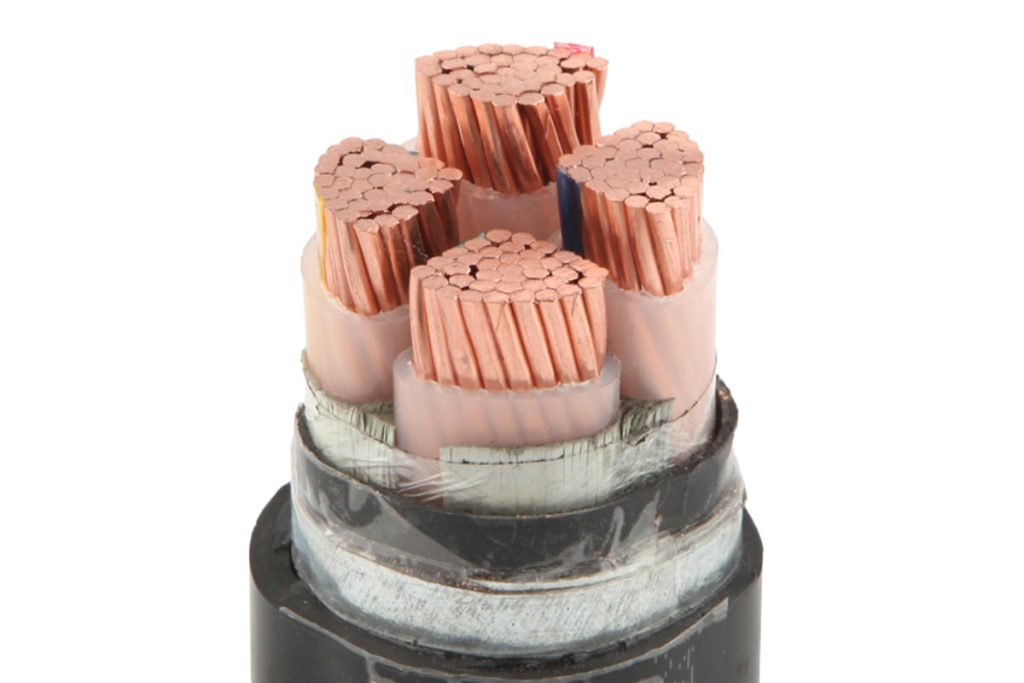
Table of Contents
- Why XLP is Preferred?
- Challenges in DC XLP Cables Technology
- Innovations in XLP Manufacturing
- Challenges in Electrical Cable Technology
- Design of Electric Field Intensity in Insulation Materials
- Determination of the Real Electric Field in Direct Current Insulation
- Advances in Research and Development
- Innovations and Future Trends in DC Technology XLP Cables
- Extended Conclusion
Why XLP is Preferred?
The choice of XLP in flexible direct current transmission technology is due to its numerous advantages:
- Lower Costs: XLP cables are cheaper to manufacture and maintain compared to traditional electrical cables.
- Greater Transport Capacity: XLP cables can handle higher volumes of power, making them ideal for modern electrical networks.
- Ease of Maintenance: Its design and material facilitate maintenance and repair operations.
Challenges in DC XLP Cables Technology
Despite its advantages, XLP faces significant technical challenges:
Research on the Properties of XLP
Research has focused on the electrical and low density properties of XLP. Nevertheless, There is a gap in studies related to the influence of microstructure and purity of LDPE. (low density polyethylene), the basis of XLP insulation.
The Microstructure of LDPE
The crystallization of polymers such as LDPE determines their mechanical and electrical resistance. Understanding how the microstructure of LDPE affects its performance is essential to improving DC XLP cables..
Impact of Terminal Double Links and Branching
LDPE is characterized by terminal double bonds and branches in its molecular structure., essential for the polyethylene cross-linking process. The balance between these factors and material properties is an important field of study..
XLP Materials Purification
Controlling space charge accumulation and nonlinear electrical conductivity under direct current fields is challenging. The purity of XLP material for cables significantly influences these properties.
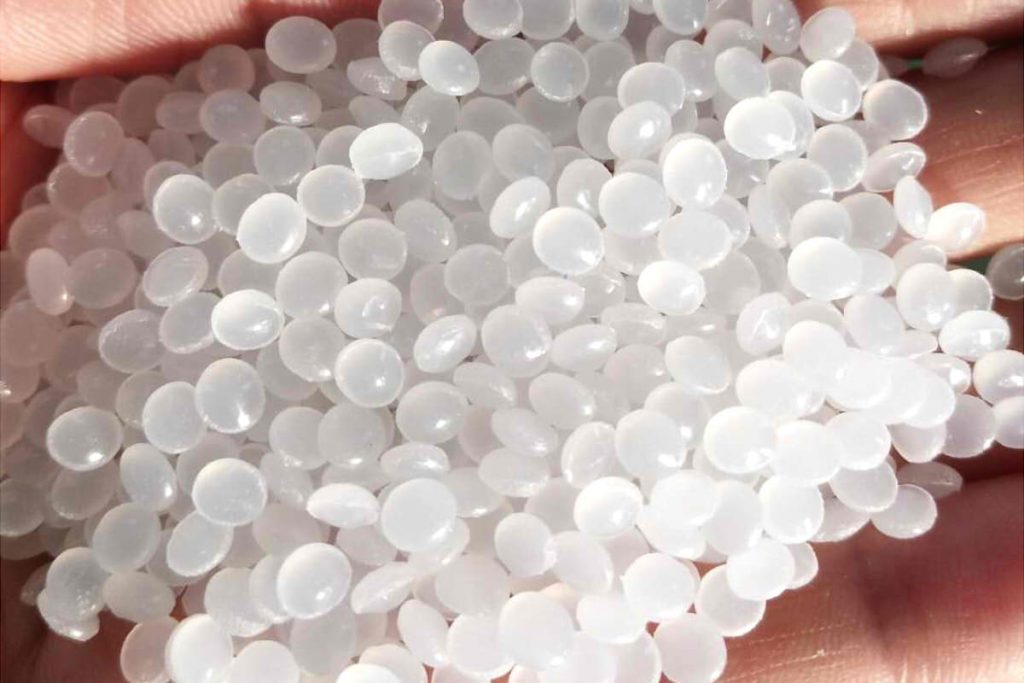
Innovations in XLP Manufacturing
Evolution in XLP manufacturing has led to significant improvements in its performance:
- Improvement in LDPE Quality: The development of high quality LDPE has been key to improving the properties of XLP cables.
- Advanced Purification Technologies: Implementation of more effective purification techniques has helped reduce impurities in XLP materials, improving your performance.
Challenges in Electrical Cable Technology
The design of the insulation structure of direct current cables differs substantially from that of alternating current cables.. The main challenges include:
- Electrical Performance Parameters: Lack of data on breaking strength and impact properties for thick insulation materials.
- Nonlinear Electrical Conductivity and Space Charge Accumulation: These phenomena complicate the determination of the electric field intensity in the insulator..
Design of Electric Field Intensity in Insulation Materials
Determine electrical parameters, as the breaking resistance in direct current, It is a complex process. Additional studies are needed to understand how the size and shape of the insulation material affect these properties..
Determination of the Real Electric Field in Direct Current Insulation
The variability of electrical conductivity with temperature and electric field intensity, as well as the accumulation of space charge, complicate the determination of the real electric field in the insulator.
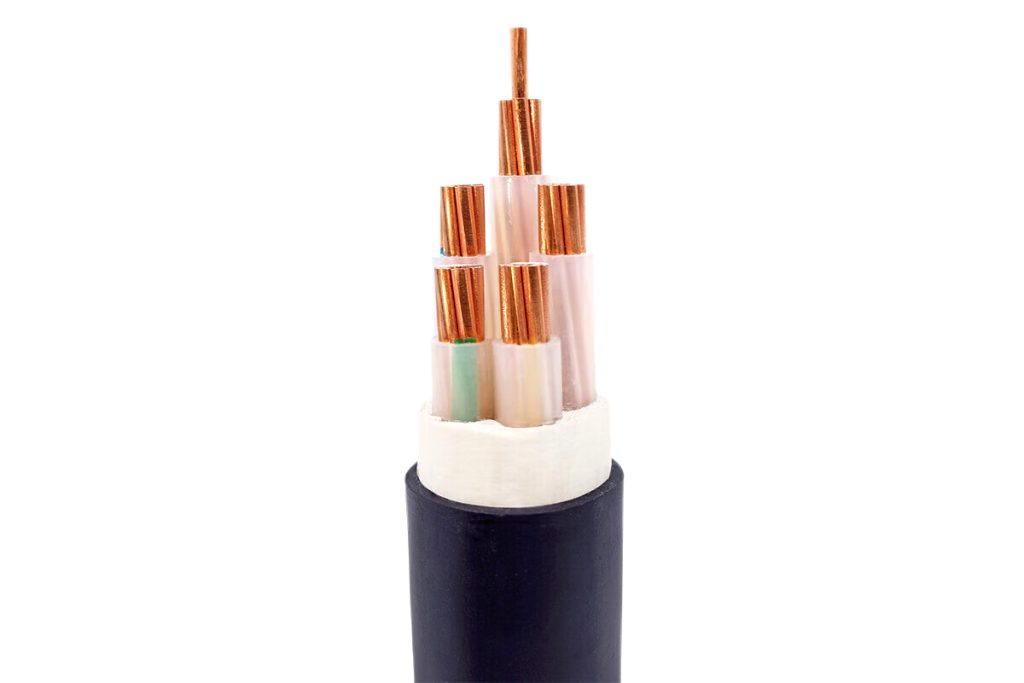
Advances in Research and Development
To overcome these challenges, Significant progress has been made in the research and development of DC XLP cables:
- Quantitative and Qualitative Models: Models are being developed to better understand the relationship between the microstructure of materials and their electrical properties..
- Advanced Measurement Technology: New measurement technologies are enabling more precise analysis of impurities and XLP quality.
- Manufacturing Process Optimization: XLP manufacturing processes are being refined to improve quality and reduce impurities.
Innovations and Future Trends in DC Technology XLP Cables
The field of DC cross-linked polyethylene cables (XLP) not only faces challenges, but is also on the threshold of several exciting innovations. These future trends are set to revolutionize the way we understand and use DC wiring..
Development of New Composite Materials
Current research focuses on developing new compounds to improve the properties of XLP.. These materials seek to optimize resistance to electrical breakdown, conductivity and thermal stability. The use of nanotechnology and nanomaterials in the XLP matrix could result in significant improvements in terms of electrical performance and durability.
Advanced Manufacturing Technologies
Advanced manufacturing technologies, such as 3D printing and additive manufacturing methods, are beginning to be explored for XLP cable production. These methods could allow for greater precision in manufacturing, optimization of cable designs and a reduction in production waste.
Intelligent Real-Time Monitoring Systems
Integrating smart sensors and systems into XLP cables could enable real-time monitoring of their performance and status. This would be essential for early detection of problems., failure prevention and predictive maintenance, thereby improving safety and operational efficiency.
Applications in Renewable Energy
With the rise of renewable energies, XLP cables are finding new applications in power transmission from renewable sources, such as wind and solar parks. Their ability to handle high voltages and currents makes them ideal for these types of applications., where efficiency and reliability are crucial.
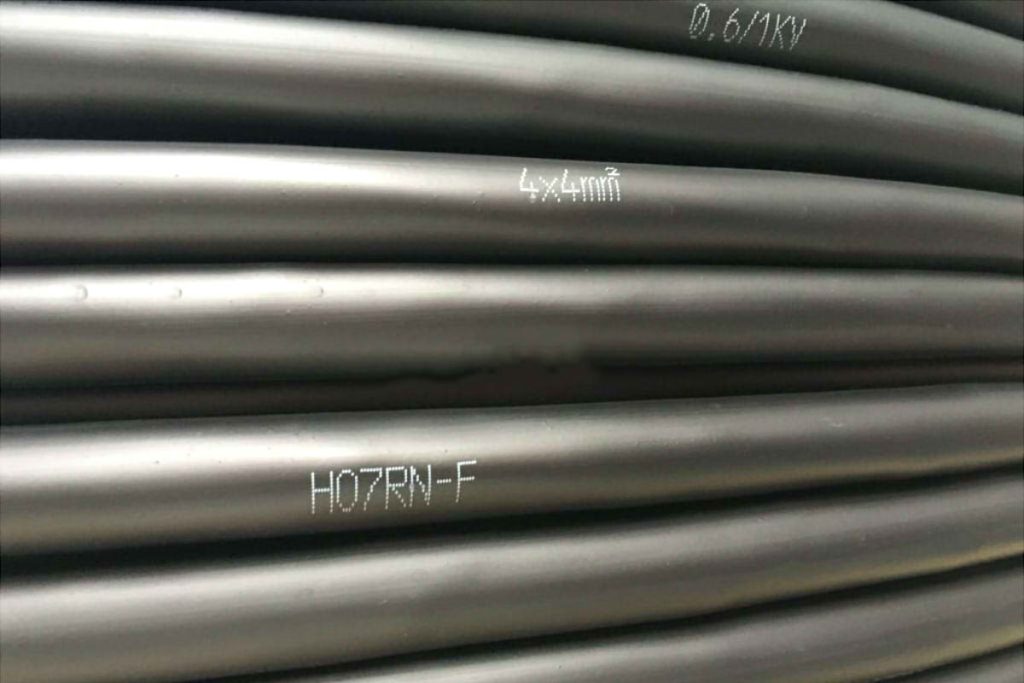
Environmental Regulations and Standards
Sustainability is a growing concern, and XLP cables are no exception. Stricter regulations and standards are being developed to ensure that the materials and processes used in the insulated cable manufacturing of XLP are environmentally friendly. This includes reducing emissions during production and developing recyclable or biodegradable materials..
International Collaboration and Unified Standards
As XLP cable gains popularity globally, International collaboration in research and development is becoming more common. Establish unified standards for manufacturing, Testing and application of XLP cables will help ensure quality and compatibility in different regions and power systems.
Extended Conclusion
XLP DC cable is a vital component in the global electrical infrastructure and continues to evolve to meet modern challenges. Innovations in materials, manufacturing technologies, monitoring systems and applications in renewable energy promise to further improve their performance and sustainability. As the world moves towards a greener, more efficient energy future, XLP DC cables are poised to play an even bigger role, driving progress in power transmission and leading the way to more advanced, greener wiring solutions.