The full name of carbon fiber conductors is Aluminum Conductor with Composite Carbon Fiber Core. (ACCC drivers). These overhead conductors They have characteristics such as high resistance, under weight, high modulus of elasticity, low expansion coefficient, bad case, reduced energy loss, high current capacity, Corrosion resistance and long service life. They are especially suitable for corrosive environments in coastal and mining areas with high levels of pollution., where drivers tend to move.
The context of the development of these conductors is because the transmission capacities of existing power lines can no longer meet the rapid growth of load. Replacing existing conductors with others of larger cross section and load capacity or building new specialized lines has become imperative..
The traditional method of dismantling old lines, Modifying towers and then installing new conductors is expensive and involves long lead times.. To address these contradictions, A project construction method has been sought that makes the most of the routes of the existing lines, Minimize the need for tower modifications and, at the same time, significantly increase the transmission capacity of the lines. In this situation, emerge ACCC cables.
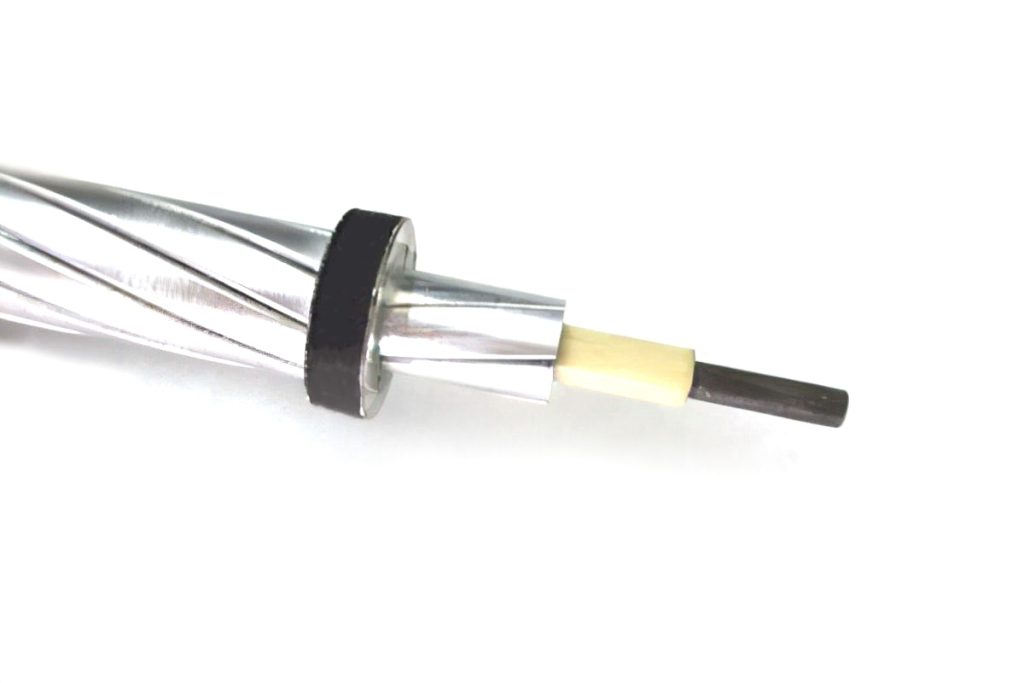
Conductive ACCCs have many advantages, but also some disadvantages. For example, most carbon fiber conductors have a simple carbon fiber core, making them prone to damage during installation. Since the damage occurs inside the stranded aluminum conductor, It is often difficult to detect and may pose security risks in its future operation. A version with a braided carbon fiber core is reportedly currently being developed.
Possible Problems in the Construction of ACCC Conductors
Type of deffect 1: Burrs on the Surface
Case Description
During the renovation and increase of capacity of an overhead transmission line HV cable for 500 kV, The steel cable with an aluminum core was replaced with carbon fiber conductors. during construction, when inspecting the conductive ACCCs with carbon fiber upon receipt, burrs were found on the surface of the conductors.
Cause Analysis
The manufacturer made defects in the production and processing process, which resulted in the appearance of burrs on the surface of the conductors.
Consequences
Once the line is up and running, Burrs can cause corona effects and tip discharge.
Suggestion
After receiving the materials, A thorough inspection must be carried out for each coil.
Type of deffect 2: Thread Breakage
Case Description
During the renovation and increase of capacity of an overhead transmission line 500 kV, The ACSR cable was replaced by ACCC cable. during construction, conductors were found to have broken wires, although no signs of stress were found during installation.
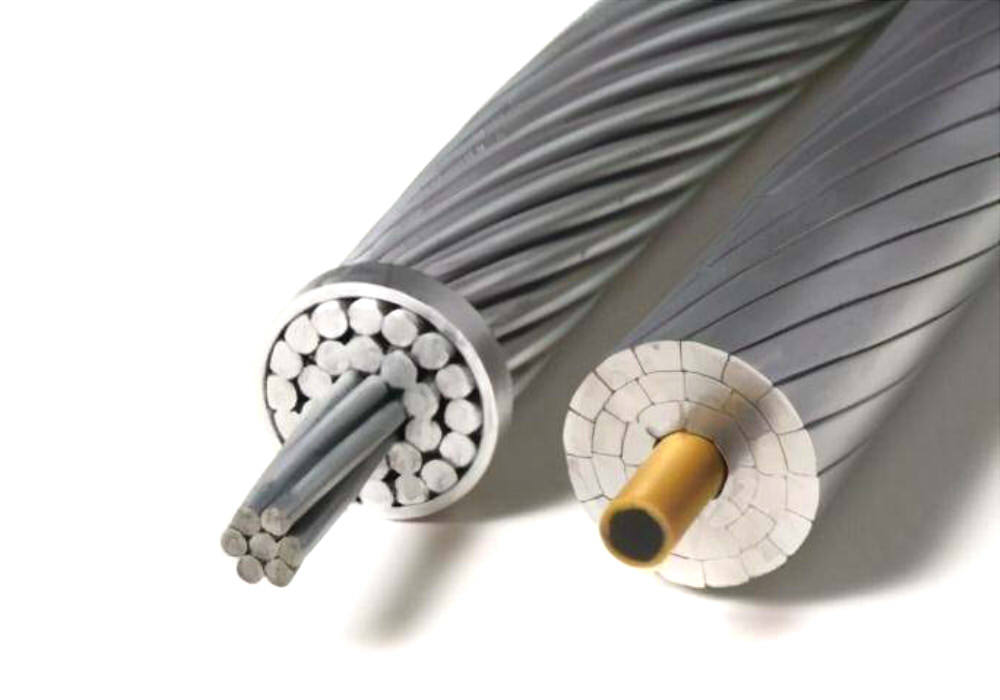
Cause Analysis
The manufacturer made defects in the production and processing process, which resulted in the conductors already having strand breaks when they left the factory.
Consequences
Once the line is up and running, These breaks can lead to scattered strands and loss of conductors..
Suggestion
After receiving the electrical materials, A thorough inspection must be carried out for each coil, paying special attention to the sections of three intersections.
Type of deffect 3: Bulging in the conductors
Case Description
During a renovation and capacity increase project on a transmission line 220 kV, The original type 1× LGJ-400/35 steel conductors with an aluminum core were replaced with type 1×JRLX/T-400 carbon fiber conductors.. During the construction of the line, a bulging phenomenon was observed in the conductors.
Cause Analysis
Carbon fiber conductors are composed of a carbon fiber inner core and a braided aluminum outer core.. During the laying or tensioning process, due to tension, The aluminum surface of the carbon fiber conductors experiences a “creep elongation”. This means that there are spaces between the aluminum strands, and the tension causes the threads to tighten together, reducing spaces. Although the length of the conductor does not change, this one stretches. Carbon fiber inner core, due to its high resistance, has minimal deformation. As a result, the outer aluminum threads and the inner carbon fiber core experience relative slip, which can lead to a bulge in the aluminum strands on the surface of the conductor.
Consequences
(1) Bulging in the aluminum strands of carbon fiber conductors is difficult to repair in operating lines, and when the aluminum threads come loose, carbon fiber core is exposed to air for long periods, which can be detrimental in harsh operating environments.
(2) After the aluminum threads bulge, Voltage variations during operation can cause uneven tensions in the surface layers of the aluminum wires., which can lead to breakage of the aluminum wires.
Suggestions
(1) Different conductor manufacturers may have different processing specifications, which can result in different voltage levels in the finished conductors. Before installation, Coordinate with the manufacturer and strictly follow their installation requirements for routing and tensioning the conductors..
(2) During construction laying and tensioning, Special pre-braiding tools should be used to reduce the use of tension heads and turnbuckles, thus avoiding the concentration of tensions.
(3) During the construction of high stress sections, before marking the section to tension, and as long as the length allows it, excess conductor on the voltage side must be cut, so that the aluminum wires that experience the “creep elongation” have the opportunity to cum at the cutting point.
Type of deffect 4: Conductor Breakage
Case Description
During a renovation and capacity increase project on a transmission line 220 kV, were replaced aluminum conductors type 2 × LGJ-300/25 steel with aluminum core by ACCC conductors with carbon fiber split type 240/30. During the construction of the line, conductor breaks occurred. All breaks occurred in the connection area of the voltage splice conductors, close tension line clamp, after installation on overhead line using pre-tensioning technique.
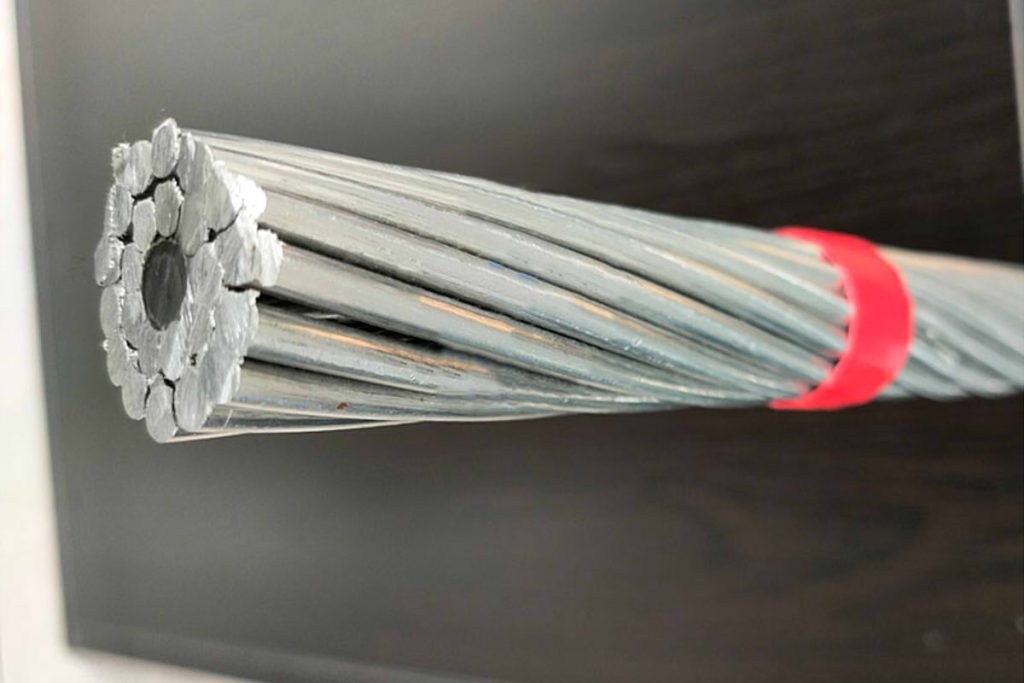
Cause Analysis
The causes of the breaks were determined through related tests and analysis of the broken tension connections. According to the test results, The main cause was that the radial crushing resistance of the carbon fiber core of the conductor did not meet the standards.
A core composed of at least 100 mm in length should be loaded uniformly at a loading speed of 1 mm/min a 21 mm/min to failure. And the composite core must withstand a pressure of at least 30 kN without cracks or detachments at the ends. Nevertheless, Tests showed that the carbon fiber conductors in this model did not meet this requirement, since the manufacturer of the carbon fiber conductors could not meet the standards regarding the radial crushing resistance of the carbon fiber cores they produced.
Consequences
conductor breakage.
Suggestion
It is recommended that during the construction of carbon fiber conductors, the regulations related to the construction technique of carbon fiber conductors with carbon fiber composite cores be strictly followed..
Type of deffect 5: Scratches on the External Surface
Defect Description
During a renovation and capacity increase project on a transmission line 500 kV, The original LGJ-400/35 steel conductors with aluminum core were replaced with JLRX/F2A-460/40-26 carbon fiber conductors.. During final inspection of the line after completion of construction, wear and cracks were discovered on the conductors.
Cause Analysis
Drivers suffered scratches and damage due to rubbing against sharp objects during transportation and installation, resulting in damage to the soft aluminum outer layer of the carbon fiber conductors.
Consequences
These defects affect the aesthetic quality of the conductors and can cause electrical corona.. In severe cases, conductors can burn and, as a last resort, cause cable breakage accidents.
Suggestion
It is recommended that a detailed inspection be carried out on each coil of conductors after their arrival at the site and an additional inspection after installation of the conductors..
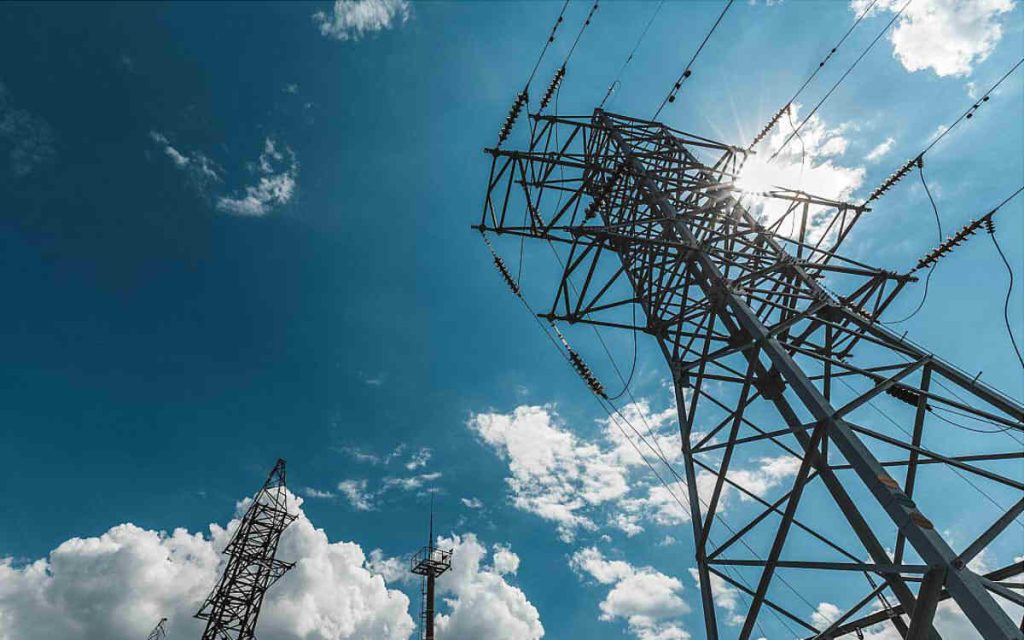
Type of deffect 6: Thread Separation
Defect Description
During a renovation and capacity increase project on a transmission line 500 kV, The original ACSR conductors type LGJ-400/35 were replaced with ACCC conductors JLRX/F2A-460/40-26. During final inspection of the line after completion of construction, sections of conductors with separated strands were discovered.
Cause Analysis
The separation of the wires in the conductors was due to two main reasons. During installation of drivers, some sections passed through pulleys with inadequate inclination angles or with pulleys that were not compatible, which resulted in excessive compression of the conductors and separation of the strands. Besides, during installation of accessories, excessive tension was applied to the conductors, which also caused the separation of the threads.
Consequences
These defects affect the aesthetic quality of the drivers, can cause electric crown Y, in serious cases, affect the resistance of conductors.
Suggestion
It is recommended that a detailed inspection be carried out on each coil of conductors after their arrival at the site and an additional inspection after installation of the conductors.. Besides, Special attention must be paid during the installation of accessories to avoid applying excessive stresses to the conductors.
Type of deffect 7: Wear
Defect Description
During a renovation and capacity increase project on a transmission line 500 kV, The original LGJ-400/35 steel conductors with aluminum core were replaced with ACCC JLRX/F2A-460/40-26 conductors.. During final inspection of the line after completion of construction, Circular wear marks were discovered on the pre-tension end of the conductors.
Cause Analysis
Circular wear on drivers was due to two main reasons. First, during the conductor pre-tensioning process, the last strands are sometimes not positioned correctly and tools such as screwdrivers are used to adjust them, resulting in scratches. Second, after pre-tension, if it is discovered that the location is not correct and the pre-tensions must be removed, adequate protective measures are often not taken, which damages the conductors during the process of removing pre-tensions.
Consequences
These defects affect the aesthetic quality of the drivers, can cause electric corona and, in serious cases, affect the resistance of conductors.
Suggestion
It is recommended to pay special attention to the inspection of conductors near pre-tension areas and strengthen protective measures during the process of removing pre-tensions to avoid damaging conductors..
Resume
Through the summary of the deficiencies found in carbon fiber conductors, Two main problems have been identified:
- Carbon Fiber Quality Issues: Due to lack of strict compliance with standards and regulations by manufacturers, products have been produced with non-compliant parameters. This has generated unpredictable risks during the construction process and during the operation of the line..
- Problems in Construction Technique: Some construction companies continue to use traditional construction methods intended for conventional drivers. This has led to problems such as bulging, wire breakage and even conductor breakage in carbon fiber conductors.
These two problems have generated significant safety risks during the operation of the lines., especially the product quality problem. According to current cases, The main problem is that carbon fiber rods do not meet regulatory requirements. Since the carbon fiber rods are the load-bearing part, Any non-conformity in the carbon rods inevitably results in a decrease in the mechanical performance of the drivers. Even if the construction technique is adequate, Breakage accidents are likely to occur in case of poor operating conditions.
Therefore, It is preferable to choose ACCC conductors from a Reliable overhead cable manufacturer like ZMS. ACCC conductors with carbon fiber, as new generation drivers, offer significant benefits for the renewal and capacity increase of power lines. It is expected that in the future, in the power line industry, be used massively for the renewal and increase of capacity of old lines.