The manufacturing of electrical cables involves a series of processes that, despite its importance for the industry, can pose significant risks to the health of workers. Next, The main jobs in this industry and the harmful factors associated with each one are described., along with recommended preventive measures.
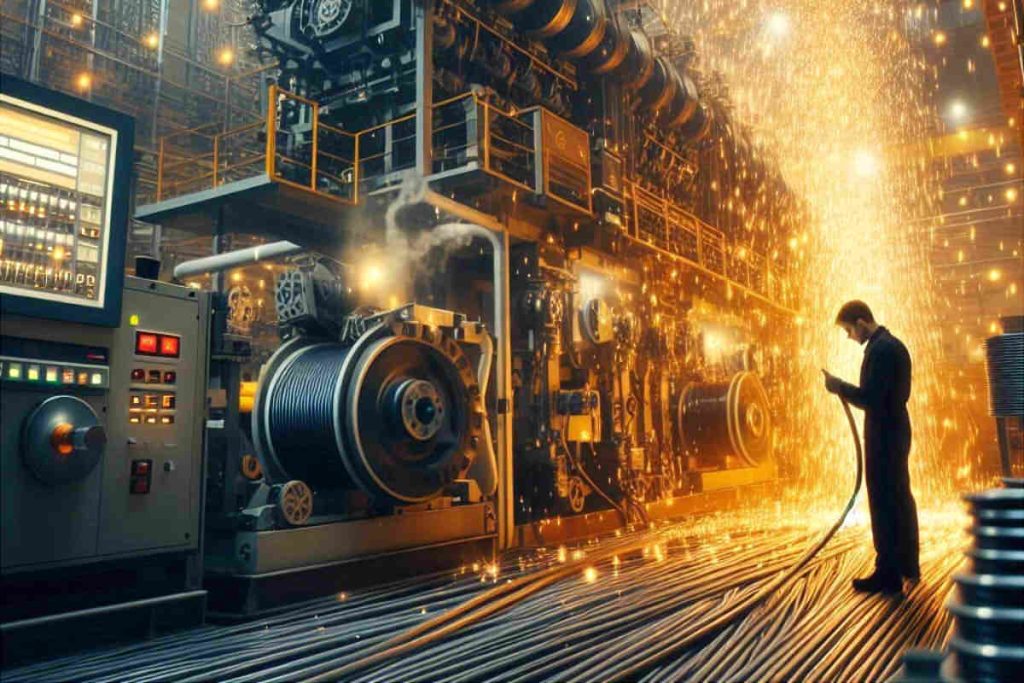
Table of Contents
- 1. Preparation of Materials for Electrical Cables
- 2. Stripping of Electrical Cables
- 3. Stretching of Electrical Cables
- 4. Heat Treatment of Electrical Cables
- 5. Tinning of Electrical Cables
- 6. Braiding of Electrical Cables
- 7. Plastic Extrusion in Electrical Cables
- 8. Rubber Extrusion in Electrical Cables
- 9. Pressing Lead into Electrical Cables
- 10. Coating with Armor
- 11. Electroplating
- 12. Drying and impregnation with oil
- 13. Spark Tests
- 14. Coating of Enameled Cables
- Prevention and Protection in the Electrical Cable Industry
1. Preparation of Materials for Electrical Cables
In this stage, aluminum or copper ingots are heated and melted to be rolled into bars. Major risks include exposure to aluminum and copper oxide dust, as well as at high temperatures. Long-term inhaled metal dust can cause lung diseases such as silicosis, while high temperatures increase the risk of heatstroke and dehydration. Las electrical cable factories must implement effective ventilation systems and dust controls, in addition to providing personal protective equipment (EPP) appropriate, such as masks and heat-resistant clothing.
2. Stripping of Electrical Cables
This process involves immersing metal bars in a sulfuric acid solution to remove oxides.. Sulfuric acid vapors are corrosive and damage the respiratory tract., eyes and skin. To mitigate these risks, strict safety regulations must be followed, using chemical protective equipment and ensuring good ventilation in work areas.
3. Stretching of Electrical Cables
Here, metal bars are stretched into wires using special molds. Harmful factors include excessive noise and metal dust, which can lead to permanent hearing loss. It is essential that employees wear hearing protection and undergo regular hearing testing.
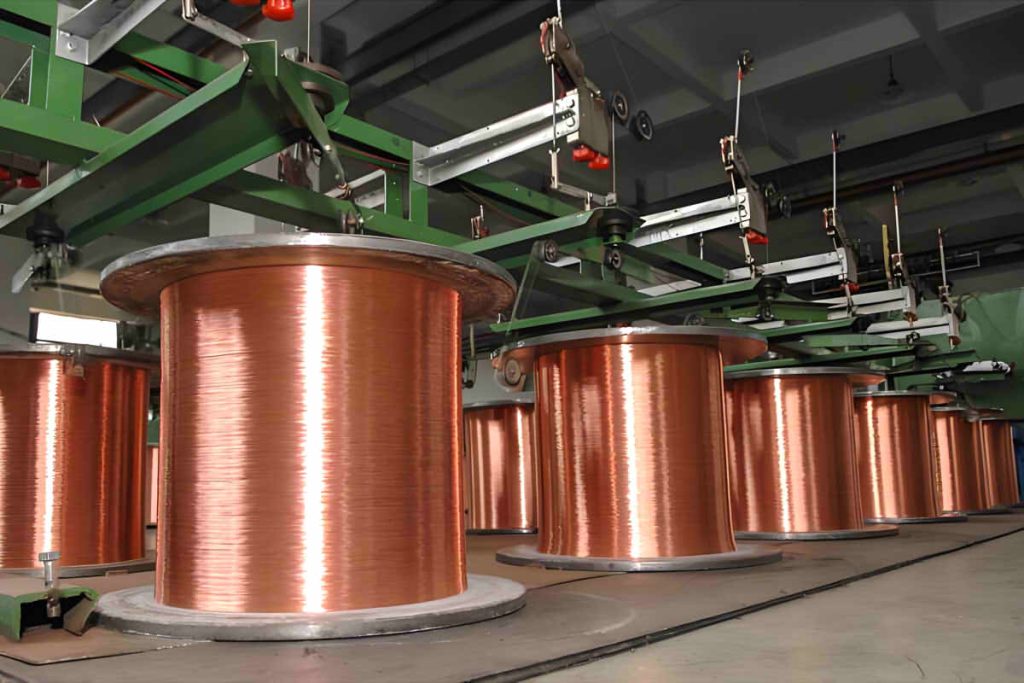
4. Heat Treatment of Electrical Cables
In this process, los conductor wires are annealed to eliminate the hardening produced by cold working. Heat is the main risk factor. Constant exposure to high temperatures can cause heat stroke. Adequate ventilation must be provided, drinking water and PPE such as heat-resistant clothing and breathable gloves.
5. Tinning of Electrical Cables
The wires are cleaned with hydrochloric acid before being dipped in hot tin to form a protective layer. Primary risks include exposure to tin fumes and hydrogen chloride.. To protect workers, It is essential to ensure adequate ventilation and provide the necessary protective equipment.
6. Braiding of Electrical Cables
This process uses machines to braid various wires and form cables. Noise is the main harmful factor. The use of noise-reducing headphones is recommended to protect workers' hearing..
7. Plastic Extrusion in Electrical Cables
during extrusion, Plastic materials such as PVC are melted and applied to the cables. The main risk is exposure to toxic gases and vinyl chloride. Closed production equipment should be used and air quality monitoring improved.
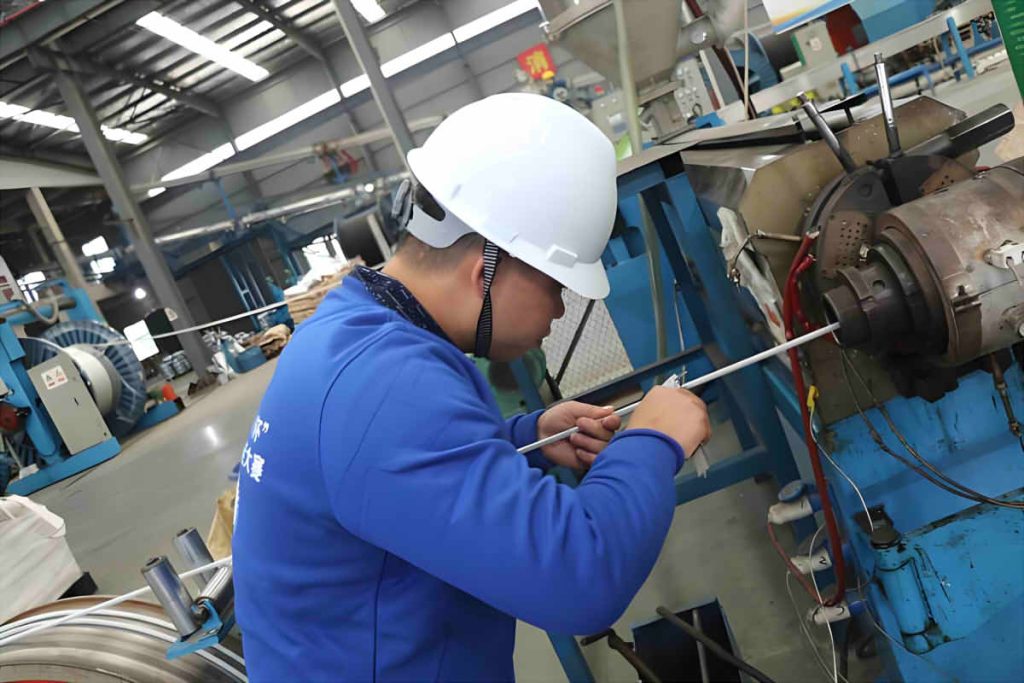
8. Rubber Extrusion in Electrical Cables
The raw rubber mixed with various components is extruded onto the rubber insulated cables to form a coating. The main risks are lime dust, clay and carbon black, along with high temperatures. It is crucial that workers wear masks and that work areas are well ventilated.
9. Pressing Lead into Electrical Cables
The process of coating cables with liquid lead involves exposure to lead dust and intense heat, which can cause lead poisoning and thermal problems. It is recommended to implement strict environmental controls and provide specialized PPE.
10. Coating with Armor
In this stage, The cables are covered with various materials such as electrical tape, jute or steel. Exposure to high temperatures and liquid tar poses health risks. It is essential to wear appropriate protective clothing and ensure good ventilation.
11. Electroplating
Los conductors are coated with silver through electrolysis, which involves the handling of cyanide and its compounds, highly toxic substances. Rigorous safety protocols must be followed to avoid exposure to these hazardous substances..
12. Drying and impregnation with oil
The cables are heated and dried before being soaked in oil. High temperatures are the main risk, Therefore, measures must be implemented to protect workers., such as ventilation and temperature control.
13. Spark Tests
In this process, cables are subjected to high voltage currents to test their insulation. The radio frequency radiation It is a harmful factor that can have thermal and non-thermal effects on health. The use of radiation protection is recommended for employees.

14. Coating of Enameled Cables
This process involves applying varnish to the wires., exposing workers to toxic compounds such as benzene and xylene. Factories need to have adequate ventilation and closed equipment to protect employees..
Prevention and Protection in the Electrical Cable Industry
The mentioned factors can cause a variety of occupational diseases, like silicosis, hearing loss, heavy metal poisoning and respiratory diseases. Electrical cable manufacturing companies have the responsibility to ensure a safe work environment by implementing technological innovations, rigorous regulatory management and the provision of appropriate personal protective equipment.
Only through effective prevention of occupational diseases and commitment to worker health can sustainable development be achieved in this key industry..