By building networks, It is essential to have a thorough understanding of the structure, materials and processes involved in the production of fiber optic cable, in order to buy adequate and excellent quality fiber optic cable.
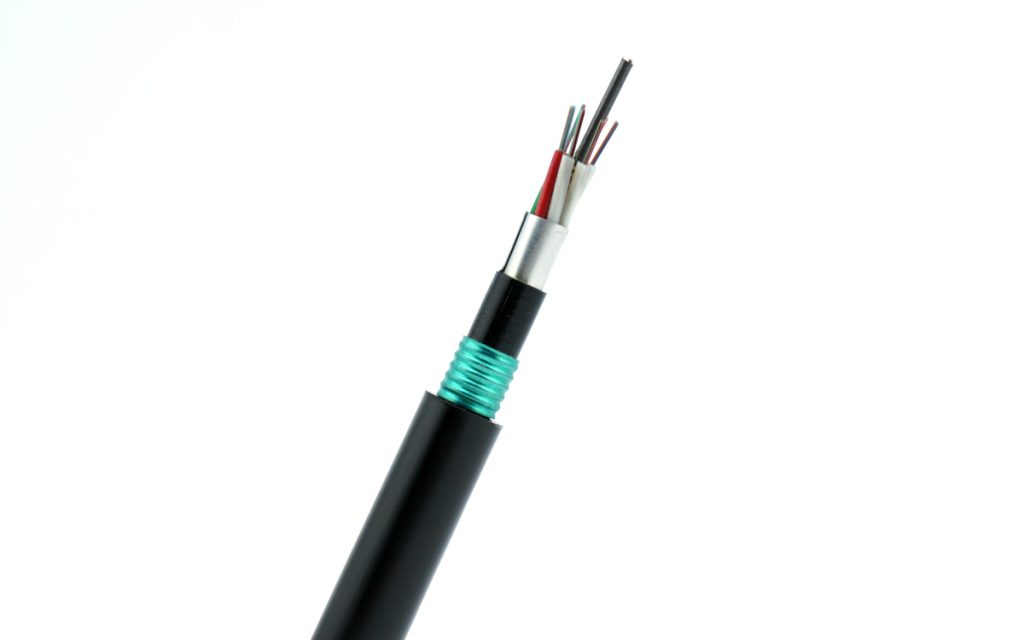
The fiber optic cable has advantages such as its reduced volume, lightness, long transmission distance, great capacity, low signal attenuation, and resistance to electromagnetic interference. It has become the main component of specialized communications networks., online data transmission, and cable tv.
Choice of Fiber Optic Cable According to the Number of Cores
The structure of the fiber optic cable is divided into several types, like the central tube, the one with skeleton, the tape and the central beam. for different purposes, different types of fiber optic cable structures are needed.
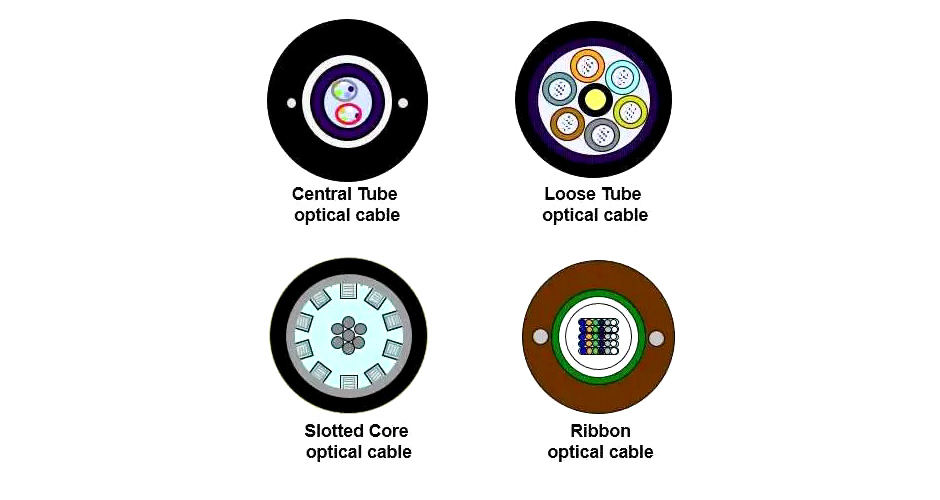
Usually, the fiber optic cable 12 cores or less uses the center beam structure. This structure is simple and low cost.. It is competitive in support and branch networks that are installed outdoors or have good conduit protection..
Skeleton structure fiber optic cable uses a steel wire or a single strand of steel wire as the core reinforcement.. can hold up to 144 cores. Its biggest advantage is its impermeability and resistance to strong pressure.. This type of cable can be buried directly in the ground. Besides, it is easy to branch, namely, when you need to use only a few optical fibers, you can cut the necessary part separately. This is beneficial for adding fiber optic nodes along the way..
The ribbon structure fiber optic cable can have more than thousand cores. The optical fibers of 4 a 12 cores are placed in a row to form a fiber optic tape drive. Then, several tape drives are arranged on the fiber optic cable according to a certain pattern. For network level cables, two types are generally used: the one with central tube and the one with skeleton.
Selection of Optical Fiber According to Its Use
Fiber optic cables can be classified into several types according to their use.: aerial, underground, buried, submarines and metal free.
Overhead cables must have high resistance and low temperature coefficient. underground fiber optics and submarine fibers must be resistant to water pressure and traction, and have a good waterproof property. Buried cables must be able to withstand pressure, moisture and chemical corrosion. Metal-free cables can be installed next to high-voltage electrical cables and their insulation must be excellent.. Although cables ADSS do not have metal reinforcing core, they must also have some traction capacity.
When buying a fiber optic cable, users should consider its use and demand from the manufacturer to ensure its stability and reliability.
Selection of Fiber Optic Cables Based on Materials
The choice of materials is important when buying fiber optic cable, as this affects the life of the cable. The manufacturing process is also a key factor affecting cable quality.. Fiber optic cable products that have a stable manufacturing process and excellent quality have minimal additional loss during production.. 0,01dB/km is a basic data to measure the quality level of the fiber optic cable manufacturing process.
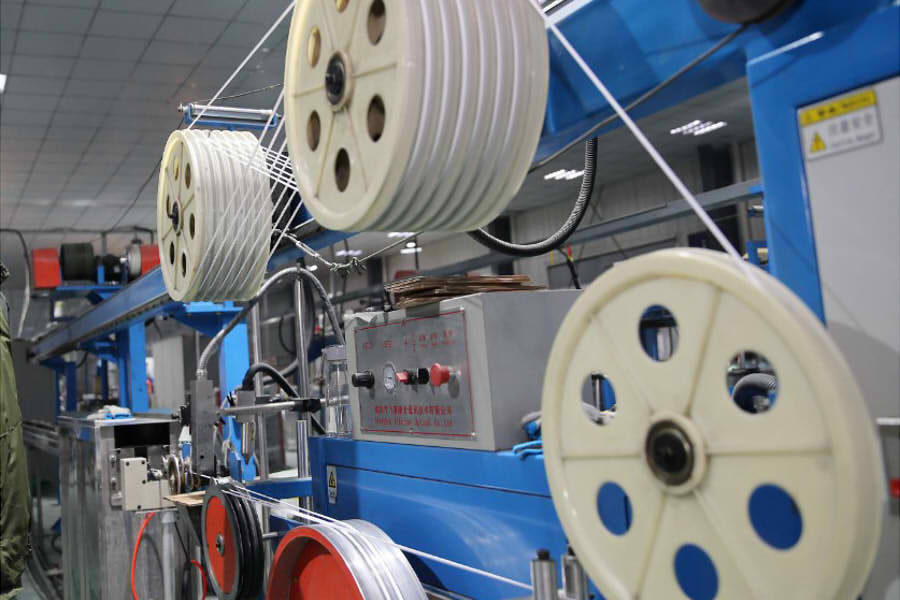
The main materials used in the fiber optic cable are the fiber core, fiber optic fat, the coating material and the PBT. Each of these materials has different performance requirements..
Fiber optic core requires significant power capacity, a signal to noise ratio alta, a low bit error rate, a long distance between amplifiers and a high information carrying capacity.
Fiber optic grease refers to the grease used to fill the fiber optic bundle tube. Its function is to dampen the vibration or impact on the optical fiber and prevent the corrosion of air humidity on the optical fiber.. Grease must meet strict quality requirements, as a very low amount of hydrogen to prevent “hydrogen loss” which can severely damage the fiber optic cable.
The lining material determines the tensile properties, flexion, temperature and natural aging resistance of fiber optic cable. A high density polyethylene material can be used (PE) for greater hardness, good tensile and compressive strength and less susceptibility to damage.
PBT is the plastic used to make the fiber optic cable bundle tube.. Must have a high Young's modulus (1600/mm2), a low coefficient of extension (1,5×10^-4), good resistance to chemical corrosion, low coefficient of friction and good processing characteristics. Using PBT to make the fiber optic sheath can make the fiber optic bundle tube with good pressure resistance and temperature resistance characteristics.. In places where high water resistance is required, a hydrolysis resistant PBT material should be used.
Choice of Appropriate Fiber Optic Depending on the Usage Environment
For fiber optic cables used in buildings, it is important to consider its fire resistance characteristics, toxicity and smoke emission. Usually, cables with a fire-resistant but smoke-emitting sheath can be used in ducts or in areas with forced ventilation. Fire resistant sheathed cables must be used., non-toxic and smoke-free in exposed environments.
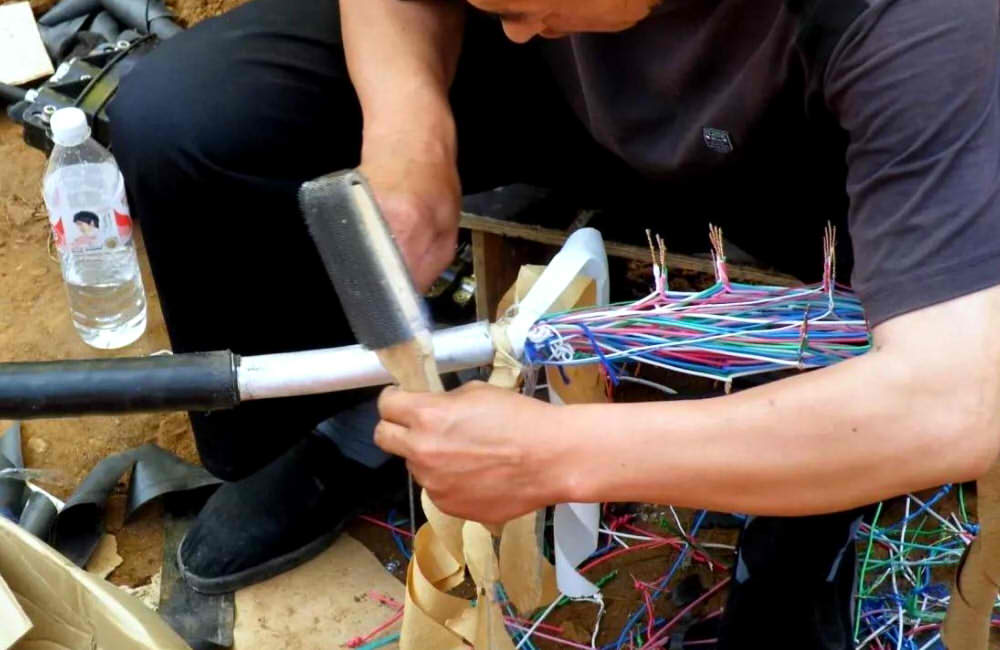
For vertical installation inside a building, layered twist fiber optic cables can be opted for. For horizontal installation, branchable fiber optic cables can be used.
And for the direct buried installation of fiber optic cables outdoors, it is recommended to use armed optical fibers. For aerial installation, ADSS or OPGW can be used.
For transmission distances less than 2 km, multimode fiber optic cables can be used. While, for distances greater than 2 km, single mode fiber optic cables or repeaters can be used.