In modern industry, the cables, as key components for the transmission of electricity and data, play an indispensable role. Whether in the operation of heavy machinery, the operation of automated production lines or in complex communication networks, High quality cables are the basis to ensure the stability and security of the systems. To ensure these critical infrastructures operate reliably, the International Electrotechnical Commission (IEC, International Electrotechnical Commission) has established unified standards to regulate the design, manufacturing and use of cables.
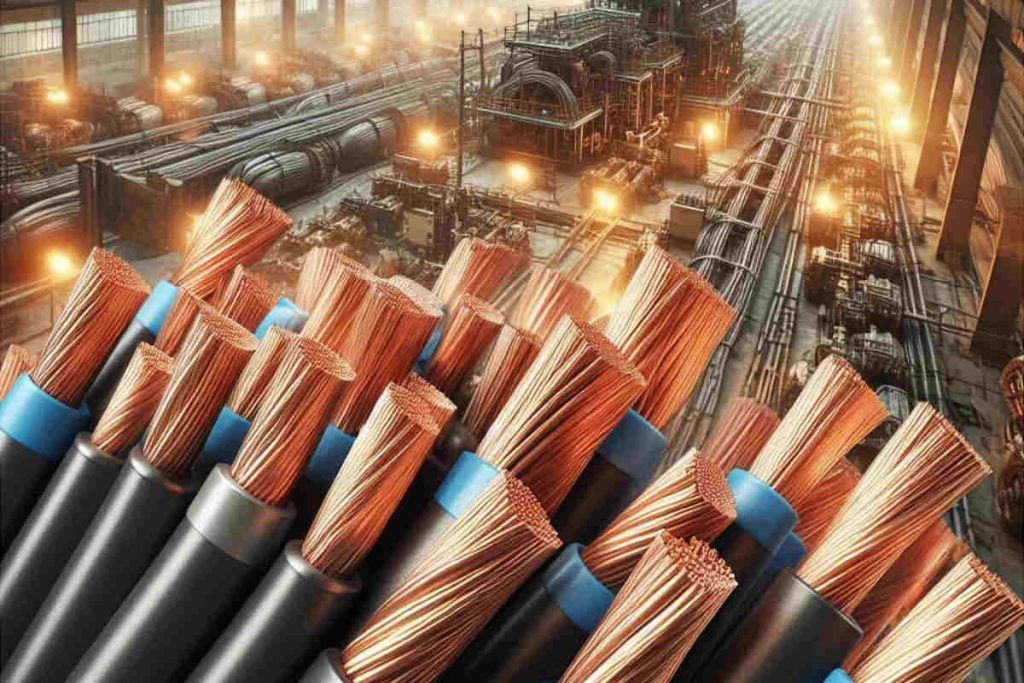
Table of Contents
- The IEC and its role in the industrial field
- The importance of industrial cable standards
- Main IEC industrial cable standards
- IEC standards and their industrial application
- IEC standards in the international market
- IEC cable references
- Conclusion
The IEC and its role in the industrial field
The IEC was founded in 1906 as a global non-governmental organization, dedicated to the preparation and publication of international electrical standards, electronics and related technologies. Through its vast network of experts, The IEC brings together professionals from around the world to participate in the standards development process. These standards cover a wide range of equipment, from household appliances to large power plants, and also cover a variety of cable products, in order to improve security, product compatibility and performance.
In the industrial field, the IEC plays a crucial role. Provides a comprehensive and rigorous system of standards that helps manufacturers produce products that meet international requirements, and offers users a reliable framework to make informed decisions. By following IEC standards, Companies can reduce operational risks, increase efficiency and promote international trade and technological exchange.
The importance of industrial cable standards
In the modern industrial environment, los high quality cables They are essential to guarantee the continuity of production. IEC cable standards are designed precisely for this purpose, establishing detailed requirements for material selection, structure design, testing methods, among others, to ensure cables work stably and durably under various harsh conditions. Besides, Standardization helps reduce failure rates, simplify maintenance processes and, as a last resort, save costs for companies.
Why are high quality cables needed in industrial environments??
- Extreme environmental conditions: Industrial facilities are often located in harsh environments, including high and low temperatures, humidity and corrosive chemicals. These conditions place extremely high demands on cable materials and structure..
- High load operation: Many industrial equipment requires operation for long periods in high power conditions., which requires cables to have high conduction capacity and heat dissipation performance.
- Security considerations: Industrial accidents can cause huge economic losses and even endanger human life.. Using cables that meet standards can significantly reduce the likelihood of electrical fires, short circuits and other safety hazards.
- Regulatory compliance: Different countries and regions have laws and regulations governing safety in industrial facilities.. Using cables that meet international standards helps companies comply with these legal requirements.
Risks and consequences of using non-compliant cables
- electrical faults: Low-quality or non-standard cables can short circuit or break., which could disrupt production and even cause fires.
- personal injuries: Defective cables may have inadequate insulation, which could cause electrical accidents and endanger the safety of operators..
- Material losses: An electrical failure can not only directly damage equipment, but also trigger a chain reaction that leads to greater property losses.
- Legal problems: Using non-compliant cables may violate local safety laws., exposing companies to fines, temporary closures or corrective measures.
Main IEC industrial cable standards
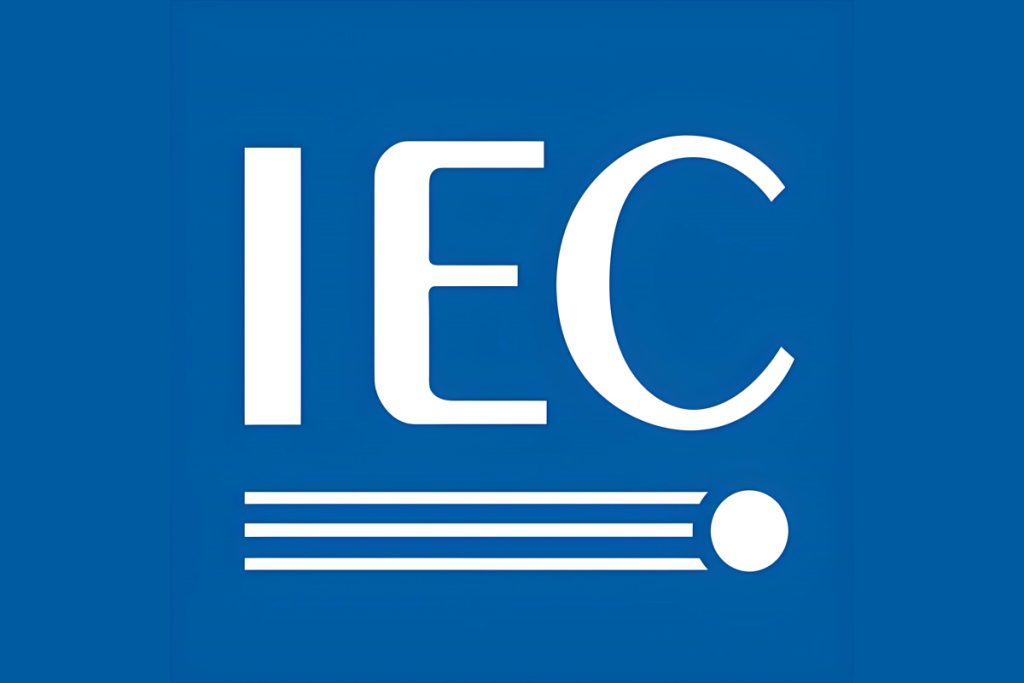
To ensure the safety and reliability of industrial cables in various demanding environments, The IEC has developed a series of detailed standards. These standards cover multiple aspects, from the size of the electrical conductors to testing methods for insulating materials. Next, Some of the main IEC industrial cable standards are presented.
IEC 60228 – conductor size
- Main content: The IEC standard 60228 specify the size, The structure and strength requirements of conductors used in electrical cables and wires. This standard includes single-core and multi-core cable conductors, applicable to bare or clad copper conductors.
- Application scenario: This standard is widely used in various power transmission and distribution systems., ensuring that conductors have adequate current rating, while maintaining good mechanical resistance and flexibility.
- Guarantee function: Standardization of conductor sizes ensures consistency between different cable manufacturers, improving system reliability and interchangeability.
IEC 60502 – Cables up to 30kV nominal voltage
- Main content: The IEC standard 60502 covers technical specifications for fixed installation high voltage cables with a nominal voltage of up to 30kV. Defines the cable structure, performance requirements, test methods and acceptance conditions.
- Application scenario: This standard applies to cables in energy transmission and distribution networks., especially in situations where high voltage transmission is required, like in substations, generating plants and large industrial facilities.
- Guarantee function: IEC 60502 guarantees the electrical and mechanical performance of high voltage cables, reducing the risk of power outages due to cable faults and improving overall system security.
IEC 60811 – Test methods for insulating materials
- Main content: The IEC standard series 60811 Provides various test methods to evaluate the performance of cable insulating materials. These tests include thermal aging, weather resistance, mechanical performance, among others, in order to verify the long-term stability and durability of materials.
- Application scenario: This standard is applicable to all types of insulating materials for cables, whether they are PVC (polyvinyl chloride), XLPE (cross-linked polyethylene) or other special materials.
- Guarantee function: Through rigorous testing, IEC 60811 ensures that insulating materials can resist environmental factors, preventing electrical leakage and short circuits, which protects both equipment and people's safety.
IEC standards provide a unified framework for cable design and manufacturing worldwide, ensuring that products from different suppliers have consistent quality and performance, making system integration and maintenance easier. Each standard includes detailed test methods and acceptance conditions to ensure that each cable is rigorously inspected before leaving the factory and meets the specific requirements of its application..
IEC standards and their industrial application
Different industrial environments present different demands regarding the use of cables. From oil and gas extraction to chemical production and mining operations, Each environment poses specific challenges and requirements. IEC standards not only provide guidance for these needs, but also ensure the reliability and safety of cables in extreme conditions through detailed specifications.
IEC cable requirements in different industrial environments
Oil and gas industry:
- Environment characteristics: High temperatures, high pressure, corrosive gases and liquids.
- Cable requirements: High temperature resistant cables are required, oils and corrosive chemicals. Besides, due to the risk of explosions, explosion-proof performance is a key factor.
- Applicable standards: Serie IEC 60079 (electrical equipment for explosive atmospheres) e IEC 60245-3 (insulated rubber cables, suitable for oil drilling rigs and other similar environments).
Chemical industry:
- Environment characteristics: Presence of strong acids, bases and other corrosive chemicals.
- Cable requirements: Cables must be highly resistant to chemical corrosion to prevent degradation from prolonged contact with chemicals.
- Applicable standards: IEC 60331 (Test methods for circuit integrity under fire conditions) e IEC 60811 (insulating materials testing methods).
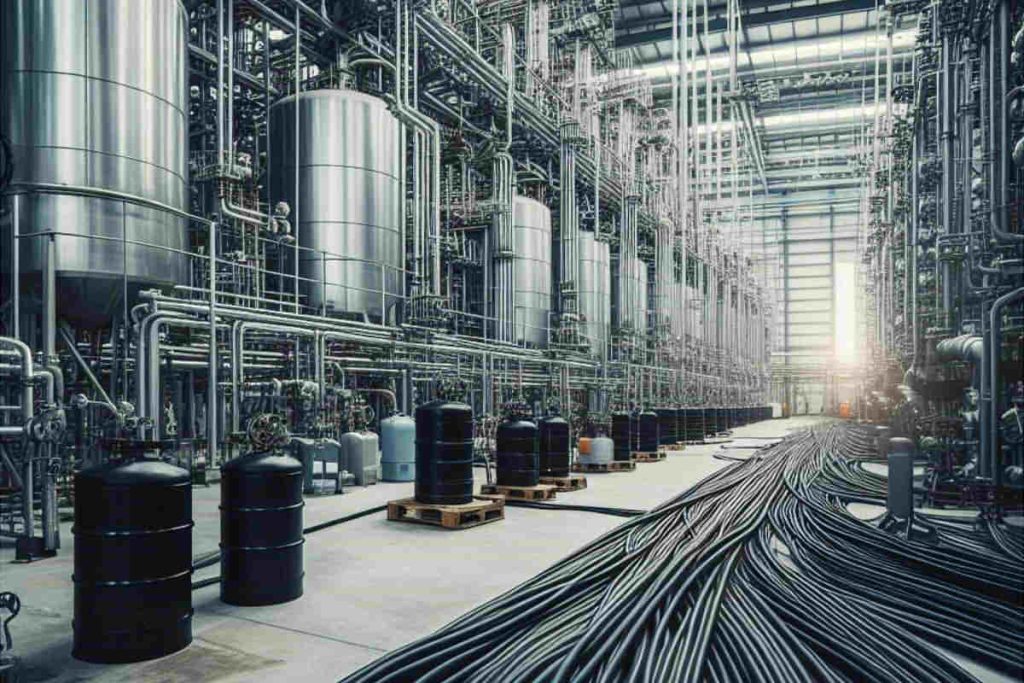
Mining industry:
- Environment characteristics: Humidity, dust, severe mechanical wear.
- Cable requirements: Los electrical cables for mining They must be waterproof, to dust and wear, and explosive atmospheres within mines must also be considered.
- Applicable standards: IEC 60332 (performance of electrical cables under combustion conditions) e IEC 60079 (electrical equipment for explosive atmospheres).
IEC cable requirements under special conditions
high temperature resistance:
- Cables operating in high temperature environments must withstand constant heat without aging or damage. An example is the cables used in steel plants or glass factories..
- Applicable standards: IEC 60216 (evaluation of thermal aging of electrical insulating materials) e IEC 60811 (insulating materials testing methods).
Explosion protection:
- In environments where there are explosive gases or dusts, cables must have explosion-proof features to prevent a spark from causing detonation.
- Applicable standards: Serie IEC 60079 (electrical equipment for explosive atmospheres).
corrosion resistance:
- In environments containing corrosive substances, The outer sheaths and insulating materials of the cables must be made of special materials that resist corrosion.
- Applicable standards: IEC 60811 (insulating materials testing methods) e IEC 60331 (Test methods for circuit integrity under fire conditions).
Analysis of practical cases: Successful projects with the application of cables that comply with IEC standards
North Sea oil field project:
- Context: The North Sea oil field is one of the largest in the world and presents an extremely adverse environment, with low temperatures, salt fog and the constant impact of waves.
- Solution: Cables that met IEC standards were used 60079 e IEC 60228, ensuring reliable operation in the demanding maritime environment.
- Results: The project was successfully implemented, and the cable system showed great stability and durability, which reduced maintenance costs and downtime.
Renovation project for a chemical plant in Germany:
- Context: A large chemical plant needed a complete upgrade of its electrical system to improve production efficiency and safety..
- Solution: Cables that complied with IEC standards were used 60332 e IEC 60811, with special emphasis on resistance to fire and chemical corrosion.
- Results: The new cable system not only improved the plant's safety levels, but also extended system life and reduced overall operating costs.
Automation project in a mine in Australia:
- Context: A large open pit mine in Australia was undergoing automated modernization to increase efficiency and safety in mining operations.
- Solution: Cables were selected that met IEC standards 60079 e IEC 60245-3, ensuring reliable transmission of power and communication under extreme working conditions.
- Results: The automation system was successfully implemented, significantly improving mine productivity and ensuring worker safety.
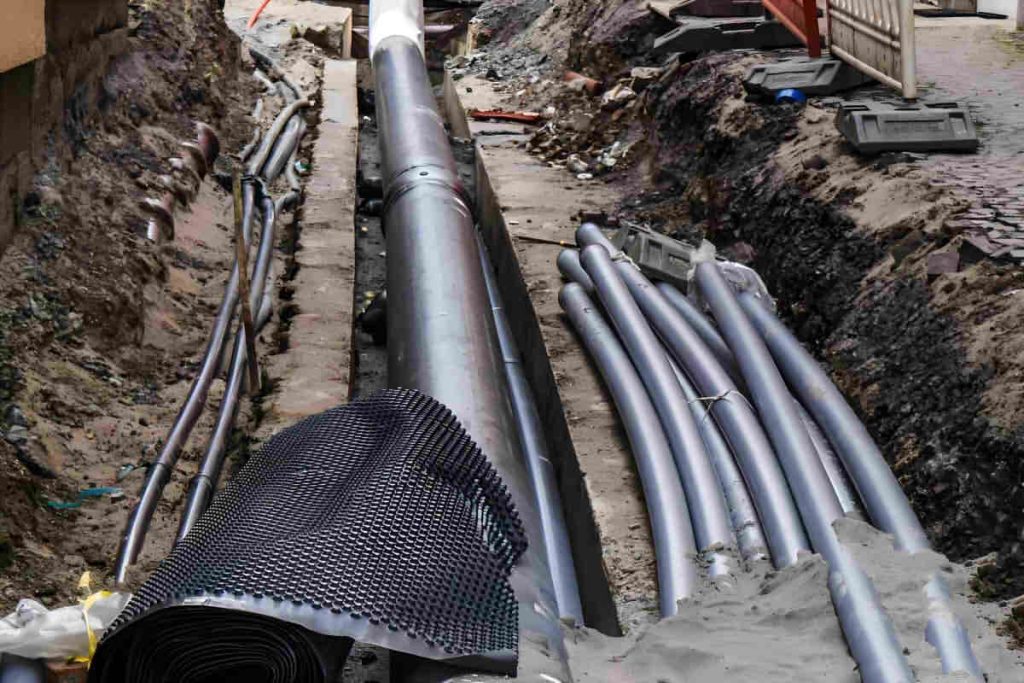
IEC standards in the international market
With the advance of globalization, The purchase and use of industrial cables are no longer limited to a single country or region. In the international market, complying with unified standards is essential. Know the degree of acceptance of IEC standards in different countries and regions, as well as the aspects to take into account in international acquisition, It is crucial to ensure the success of projects.
Acceptance of IEC standards in different countries and regions
Europa:
- European countries widely adopt IEC standards, and through CENELEC (European Committee for Electrotechnical Standardization), These standards are transformed into EN standards (European standards). For example, the EN standard 60502 is based on the IEC standard 60502.
- Within the European Union, Products that meet IEC standards are generally considered safe and reliable, which facilitates its circulation in the market.
North America:
- UL standards predominate in North America (Underwriters Laboratories) and C.S.A. (Canadian Standards Association). Although these standards differ from the IEC, many manufacturers comply with both to expand their presence in the market.
- In recent years, North America has begun to adopt more IEC standards, especially in the context of international trade, which helps simplify certification processes.
Asia:
- Asian countries like China, Japan and South Korea are also actively adopting IEC standards. For example, many GB/T series standards in China are based on IEC standards.
- In Southeast Asia, Countries like Thailand and Malaysia are also taking IEC standards as a reference, especially in the energy and telecommunications sectors.
Other regions:
- In Africa and South America, IEC standards are widely recognized, particularly in countries that actively participate in international trade. Nevertheless, some developing countries are in the process of refining their national standards systems, which can generate the coexistence of local regulations in certain regions.
Important Considerations in International Acquisition

Certification and compliance:
- Checks whether the supplier's products comply with the rules and regulations of the target market. For example, In the European Union, products must have the CE mark, while in the United States they may require UL certification.
- Make sure you know and comply with local import regulations, including tariffs and possible technical barriers.
Quality control:
- Select reputable suppliers that are certified by independent organizations. Make sure they can provide test reports and detailed technical specifications.
- Consider sending technical personnel to carry out on-site quality inspections or hiring local professional agencies for product verification.
Logistics and supply chain management:
- Evaluate delivery times, transportation methods and supplier costs to ensure on-time delivery and cost control.
- Identify potential risks in the supply chain, such as political instability or natural disasters, and establish contingency plans.
Complying with IEC standards allows companies to take advantage of opportunities in the international market and gain competitive advantages. Consistency in standards is key to guarantee product quality, reduce risks and improve efficiency. Thus, During international procurement it is crucial to focus on regulatory compliance to ensure successful project implementation.
IEC cable references
Here are some cable references corresponding to IEC standards. These standards specify the technical characteristics of cables for different applications., ensuring its performance and safety in diverse industrial environments.
- IEC 227-01: Unsheathed single core cables with solid conductors for general use.
- IEC 227-02: Unsheathed single core cables with flexible conductors for general use.
- IEC 227-05: Single core unsheathed cables with solid conductors resistant to temperatures up to 70°C.
- IEC 227-06: Single core unsheathed cables with flexible conductors resistant to temperatures up to 70°C.
- IEC 227-07: Single core unsheathed cables with solid conductors resistant to temperatures up to 90°C.
- IEC 227-08: Single core unsheathed cables with flexible conductors resistant to temperatures up to 90°C.
- IEC 227-10: Lightweight cables with PVC insulation and sheath.
- IEC 227-41: Flexible flat cables with copper jacket.
- IEC 227-42: Unsheathed Flexible Flat Cables.
- IEC 227-43: Flexible cables for indoor decorative lighting circuits.
- IEC 227-52: Lightweight flexible cables with PVC coating.
- IEC 227-53: Standard Flexible PVC Sheathed Cables.
- IEC 227-71f: Flat elevator cables and flexible connections with PVC insulation and coating.
- IEC 227-74: Flexible armored cables with oil-resistant PVC jacket and PVC insulation.
- IEC 227-75: Unshielded flexible cables with oil-resistant PVC jacket and PVC insulation.
- IEC 245-03: Cables with silicone rubber insulation resistant to temperatures up to 180°C.
- IEC 245-04: Unsheathed single core cables with ethylene-vinyl acetate rubber insulation or equivalent synthetic elastomers, resistant to temperatures up to 110°C and with a voltage of 750V.
- IEC 245-05: Unsheathed single core cables with ethylene-vinyl acetate rubber insulation or equivalent synthetic elastomers, resistant to temperatures up to 110°C and with a voltage of 750V.
- IEC 245-06: Unsheathed single core cables with ethylene-vinyl acetate rubber insulation or equivalent synthetic elastomers, resistant to temperatures up to 110°C and with a voltage of 500V.
Conclusion
IEC standards provide a unified framework for design, manufacturing and use of cables worldwide, ensuring superior performance in extreme conditions. IEC cable standards not only reflect the current technological level, but also promote the development of new technologies. As new materials and processes emerge, standards are continually updated, encouraging manufacturers to innovate to offer more efficient and environmentally friendly products.