Electrical cables and wires, as important means of transmitting energy and signals, have a quality that directly affects the safe and stable operation of the electrical system. Therefore, Cable and wire inspection can ensure that it meets technical standards and requirements. This is an important responsibility of wire and cable manufacturers..
Table of Contents
- Inspection of dimensions and structure of the appearance of electrical cables and wires
- Inspection of electrical performance of electrical cables and wires
- Mechanical performance testing of electrical cables and wires
- Inspection of the manufacturing process of electrical cables and wires
- Conclusion
The finished product inspection of electrical cables and wires is mainly divided into: appearance dimensions and structure inspection, inspection of electrical performance of cables and wires, and inspection of mechanical performance of cables and wires.
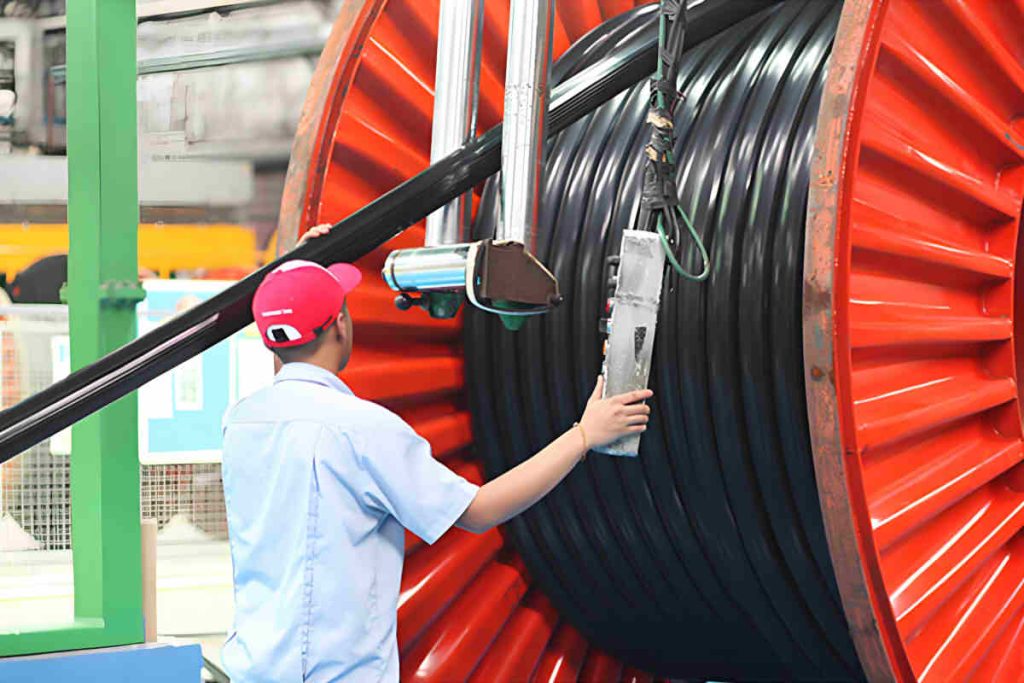
Inspection of dimensions and structure of the appearance of electrical cables and wires
The inspection of dimensions and structure of the appearance of electrical cables and wires is the first quality control project of electrical cables and wires, and can be subdivided into: appearance inspection, dimension inspection and structure inspection.
Appearance inspection
Appearance inspection of electrical cables and wires should ensure that their surface is round and smooth., no burrs, cracks, stains, oil or other defects and impurities that may affect its normal operation. Besides, It must be guaranteed that its degree of corrosion and oxidation meets the requirements.
Dimension inspection
Dimension inspection includes outside diameter, thickness, eccentricity, fan-shaped section height, paso, cross section and density. It is necessary to carry out sampling inspection of the thickness of the insulating layer and the diameter of the wire. The sampling method must take a wire sample at at least three points with an interval of 1 metro, then measure it with a micrometer. The thickness of the insulating layer of various cables and electrical wires should not be less than the relevant requirements, and the diameter error of various wires should not be less than 1% of the nominal diameter.
Structure inspection
The structure inspection of electrical cables and wires can be divided into section inspection, deck inspection, cable core structure inspection and insulating core inspection. Inspection of the structure is, in fact, a combination of appearance inspection and dimension inspection, ensuring both that the appearance is free of defects and that the dimensions are basically correct.
Inspection of electrical performance of electrical cables and wires
The electrical performance of electrical cables and wires constitutes a large part of their quality, and its proper functioning directly affects the use of cables. It is mainly divided into direct current resistance test, voltage test and insulation resistance test.
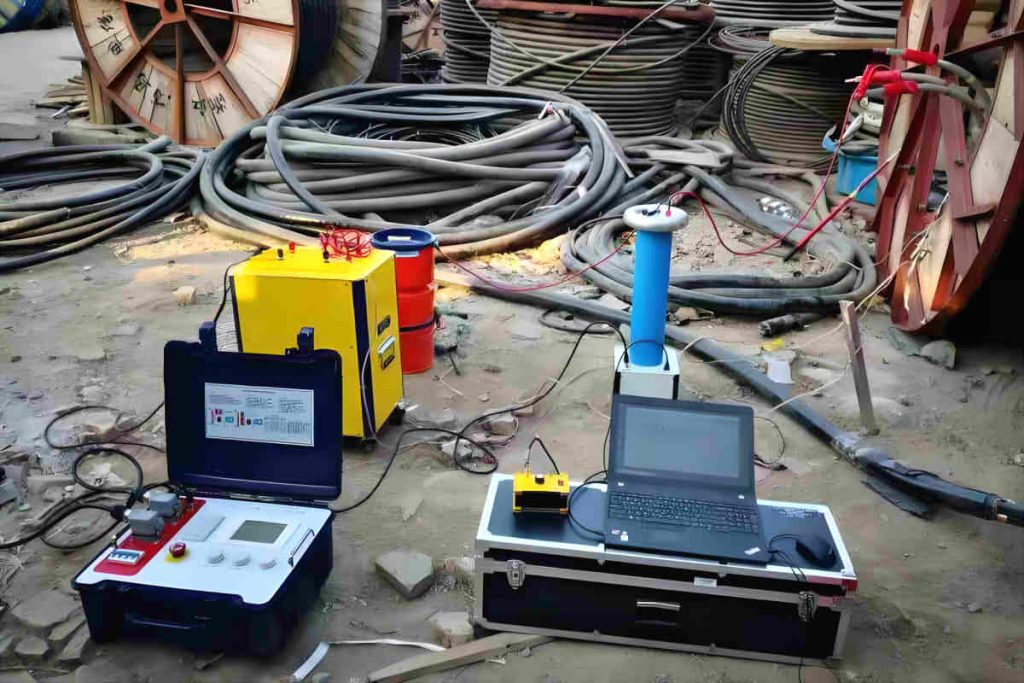
DC resistance test
Direct current resistance test is carried out according to the law of resistance, namely, R = ρL/S, where ρ is the resistivity, L is the length of the conductor and S is the cross-sectional area of the conductor.
Testing method: DC resistance measurement is performed using a single-arm or double-arm DC bridge. Measuring range: double arm bridge measures 1Ω and below, Single-arm or double-arm bridge measures 1Ω to 99.9Ω, single arm bridge measures less than 100Ω.
Conversion of standard DC resistance at 20℃: R20 = 1000Rx / [1 + a (t – 20)] L, where R20 is the direct current resistance at 20℃/km, Rx is the measured value, α is the temperature coefficient of the resistance and L is the measurement length of the sample. When performing the resistance test, The following points should be taken into account: The temperature variation of the test environment should not be greater than ±1℃, The temperature of the test environment should be measured with a thermometer at least 1 m from the ground and no more than 1 sample m, and the appropriate current density during measurement should generally be no greater than 0.5 A/mm² for aluminum conductors and not greater than 1 A/mm² for copper conductors.
Voltage test
The insulation resistance of electrical cables and wires depends on the capacity of their insulation structure and the insulation materials to withstand the electric field without breaking down. To ensure the safe operation of electrical cables and wires, A voltage test is usually performed. Voltage test: under specific conditions, A certain voltage is applied to the product for a certain time to check whether an electrical breakdown occurs, which indicates whether the sample meets the standards. Voltage and test time can be selected according to the product. When performing the voltage test, Care should be taken to ensure that the testing area has a grounded metal railing., complete emergency protection measures, a ground electrode in the test area and a ground resistance of less than 4Ω.
Insulation resistance test
Insulation resistance is an important indicator of the insulation characteristics of electrical wire and cable products., reflecting the product's ability to withstand electrical or thermal breakdown, as well as the ability of the insulation material to resist losses under working conditions. Insulation resistance refers to the relationship between the direct current voltage U applied to the insulation and the leakage current Ig, namely, R i = U/Ig. The most commonly used test methods are the direct current comparison method and the voltage and current method. In testing, you can choose model ZC-90 insulation resistance tester or other similar testing equipment.; the effective length of the sample, the test environment and test voltage must meet the corresponding standards. Calculation of the final test result: RL = RX·L, where RL is the insulation resistance per kilometer of length, RX is the insulation resistance of the sample and L is the effective length of the measured sample.
Mechanical performance testing of electrical cables and wires
Electrical cables and wires must possess certain mechanical properties according to production requirements, transportation and use. These properties mainly include mechanical resistance tests, flexibility tests, twist tests and winding tests.
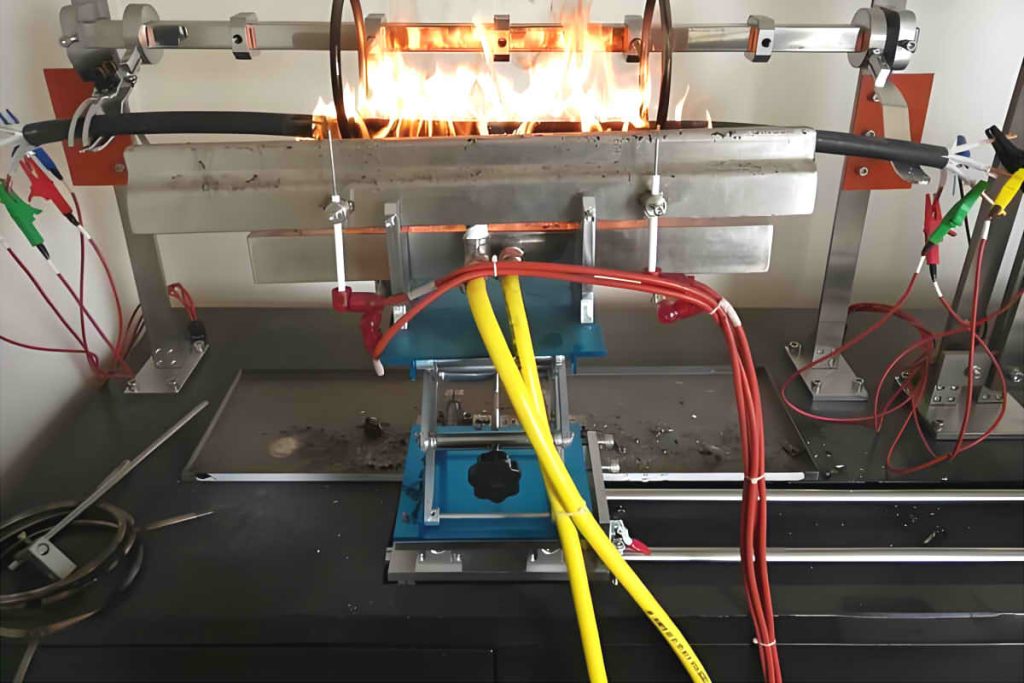
Mechanical resistance tests
The capacity of a cable to resist external forces without suffering damage is called mechanical resistance. Mechanical strength requirements mainly include tensile strength and elongation. Specific testing methods are based on the tensile strength formula: δ = Fm/S and the elongation at break formula: c = (L1 – L0) / L0× 100%. Common mechanical strength tests on cables include the resistance and elongation of copper and aluminum wires., and the strength and elongation of insulation and covering materials before and after aging.
Flexibility tests
The bending stresses that electrical cables and wires endure during production and use directly affect the quality and life of the product.. Flexibility performance depends on the number of times the product can be bent, namely, the total number of times a material sample is continuously and uniformly bent on a bending testing machine until it breaks.
Torsion tests
Twist test is an important measure to determine the plastic deformation of metal wire under the action of twisting and to judge whether the metal structure is uniform and free of defects.. Twist testing can determine whether the wire meets usage requirements based on the number of twists before breaking.
winding tests
Electrical wire and cable product standards stipulate that metal wires must have good winding properties. The winding test method involves winding the sample around a test rod of specified diameter a specified number of turns and observing the changes on its surface.
Inspection of the manufacturing process of electrical cables and wires
Although the manufacturing process of electrical cables and wires is not very complicated, includes numerous steps. According to the manufacturing process, can be divided into: drawn, annealing, conductor braiding, insulation extrusion, among others more than 10 Steps. To guarantee the final quality of the product, Every step of the process must have scientific and complete inspection methods, generally divided into: self-inspection during work, mutual inspection, patrol inspection and final inspection. Los wire and cable manufacturers must have a complete quality system to ensure that each production process goes through strict procedural inspections.
Conclusion
In summary, Inspection of electrical cables and wires is a crucial step to ensure product quality. When testing on multiple cable performance indicators, Potential security risks can be effectively prevented and eliminated, providing a strong guarantee for the safe and stable operation of the electrical system.