Cable vulcanization is a crucial step in the cable manufacturing process.. The main objective of this procedure is to improve the physical and mechanical properties of the rubber used as insulation.. Vulcanization involves the crosslinking of rubber molecules into a three-dimensional network through external shearing and high temperatures.. This process gives the rubber greater tensile strength., toughness, ability to resist aging and elasticity.
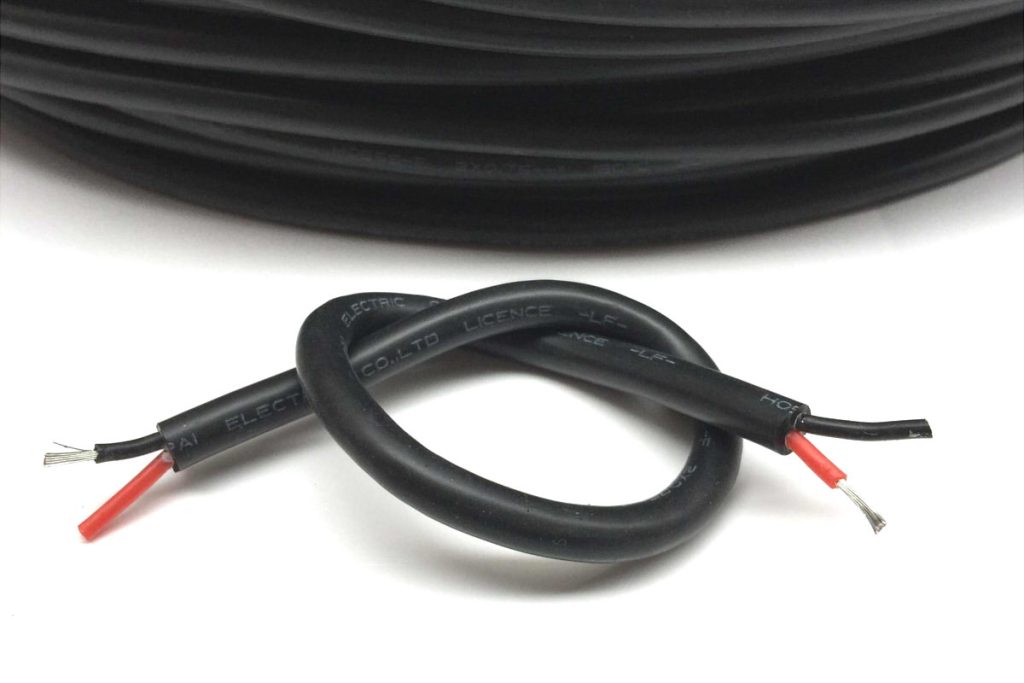
Table of Contents
- Vulcanization Concept
- Vulcanization Course
- Cable Vulcanization Process
- Advantages of Vulcanized Cables
- PVC Cables Vulcanizados: Another Common Option
- Conclusion
Vulcanization Concept
Vulcanization is the result of a chemical reaction between raw rubber and a vulcanizing agent present in the rubber material.. Under hot conditions, This reaction transforms the rubber molecules from their linear structure to a reticulated structure three-dimensional. This change in the molecular structure of the rubber significantly improves its physical and mechanical properties., as well as other features.
With the advancement of production, Vulcanization no longer requires high temperatures or vulcanizing agents. High energy irradiation and some types of rubber allow vulcanization at much lower temperatures, and even at room temperature. Therefore, The broad concept of vulcanization involves the cross-linking of rubber under specific conditions, transforming rubber macromolecules from a linear to a cross-linked structure.
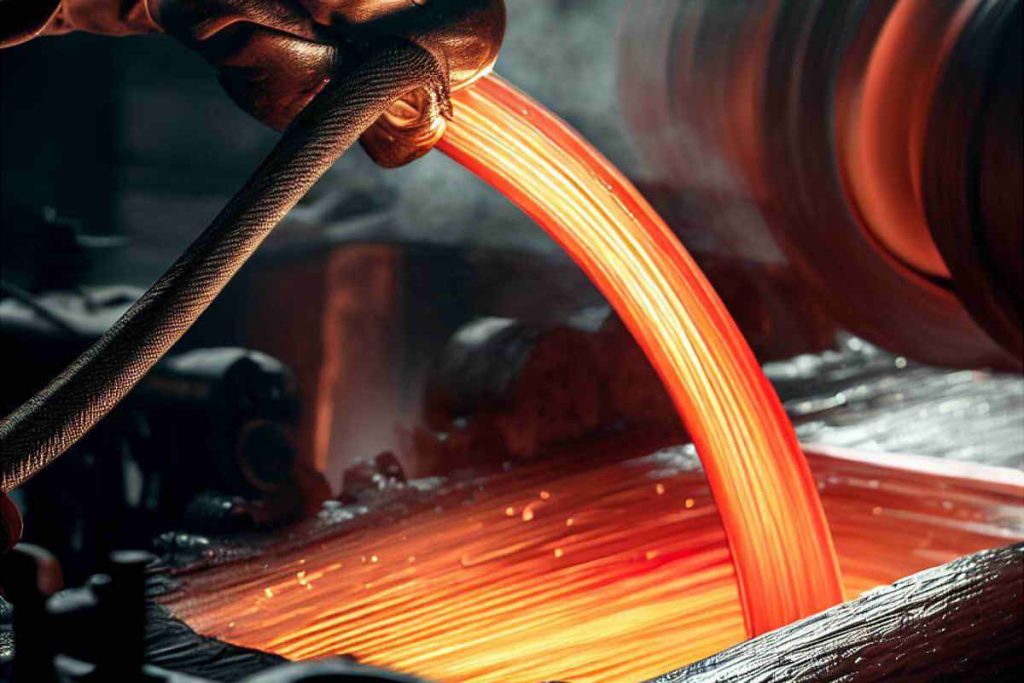
Vulcanization Course
The vulcanization curve describes how the properties of rubber change over time during the vulcanization process.. Based on the determination of the tensile strength of rubber, This process is divided into four stages: the vulcanization induction stage, the pre-curing stage, the positive curing stage and the overcuring stage.
The induction phase of vulcanization is also known as the initial phase of vulcanization.. The pre-curing phase is when the rubber begins to vulcanize.. And the positive curing phase is also known as flat vulcanization phase. The overcuring phase, for his part, It is the main phase of oxidative chain breakage.
Cable Vulcanization Process
In the process of rubber cable manufacturing, Vulcanization is carried out by extruding or impregnating the original rubber with a vulcanizing compound. After vulcanization, impregnation and drying, proceed to the following steps. Different combinations of materials are used, as “vulcanizing agent + material”, “vulcanizing agent + additions + general agent”, “vulcanizing agent + filling”, among others.
There are three main methods of vulcanization: cold vulcanization, room temperature vulcanization and hot vulcanization. Most rubber products are hot vulcanized. Equipment used for hot vulcanization includes vulcanizing tanks and flat vulcanizers.. In the case of the rubber cables, The continuous vulcanization process using hot air is mainly used..
Continuous vulcanization process parameters can be calculated in advance using mathematical models to determine appropriate production specifications, the required muzzle velocity, the proper vapor pressure and the maximum vapor pressure.
Continuous vulcanization has evolved from traditional extrusion and tank vulcanization methods., and offers many advantages, such as increased productivity and superior appearance of cables and wires. Besides, prevents oxidation of copper conductors, among other benefits.
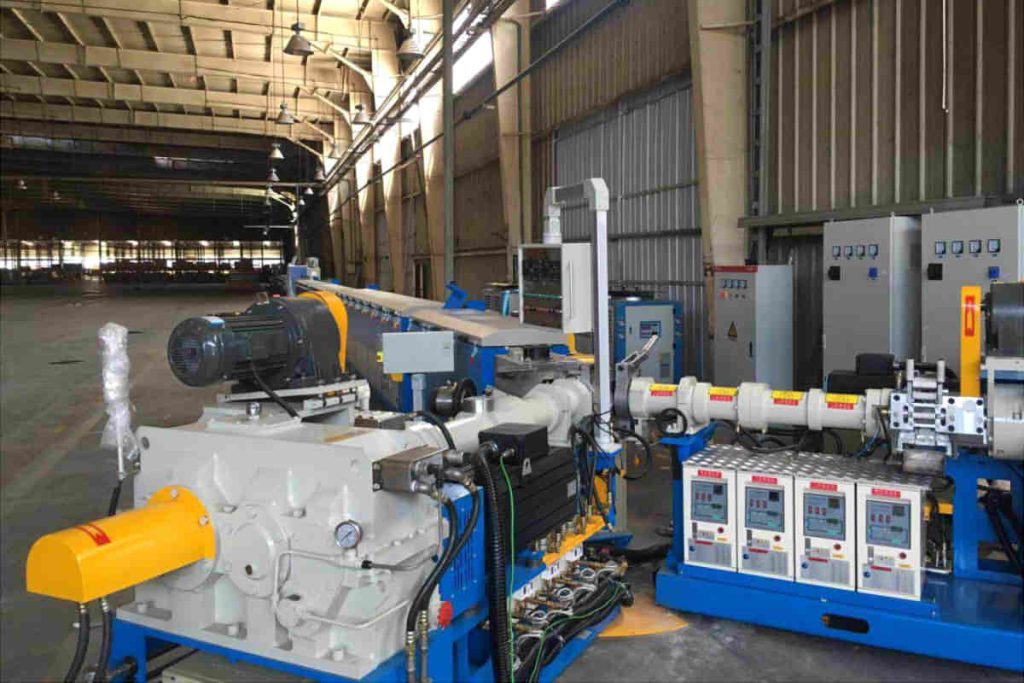
Advantages of Vulcanized Cables
Currently, vulcanized cables have replaced some cross-linked polyethylene cables. Its investment costs are higher than those of pure PVC insulation, but the performance improves a lot.
Improved resistance
Vulcanization improves the resistance of rubber, resulting in cables that are more durable and able to withstand harsh conditions. Vulcanized cables are less prone to abrasion damage, impact or deformation, making them ideal for demanding environments.
Longer useful life
Vulcanization extends the life of cables by increasing their resistance to aging and degradation. Vulcanized cables are less susceptible to external factors such as UV radiation, humidity and chemicals, allowing them to maintain their performance over time.
Performance in extreme conditions
Vulcanized cables offer exceptional performance in extreme temperature conditions, whether in high or low temperatures. They maintain their flexibility and dielectric properties even in extreme heat or cold environments, guaranteeing a reliable and safe electricity supply.
Resistance to humidity and chemical agents
Vulcanized cables are highly resistant to humidity and various chemical agents.. This makes them suitable for applications in environments where resistance to corrosion and exposure to aggressive chemicals is required..
Better electrical performance
Vulcanized cables offer excellent electrical performance, with low resistance and dielectric loss. This makes them ideal for applications that require efficient transmission of electrical energy., such as in power distribution systems or in high-power industrial installations.
PVC Cables Vulcanizados: Another Common Option
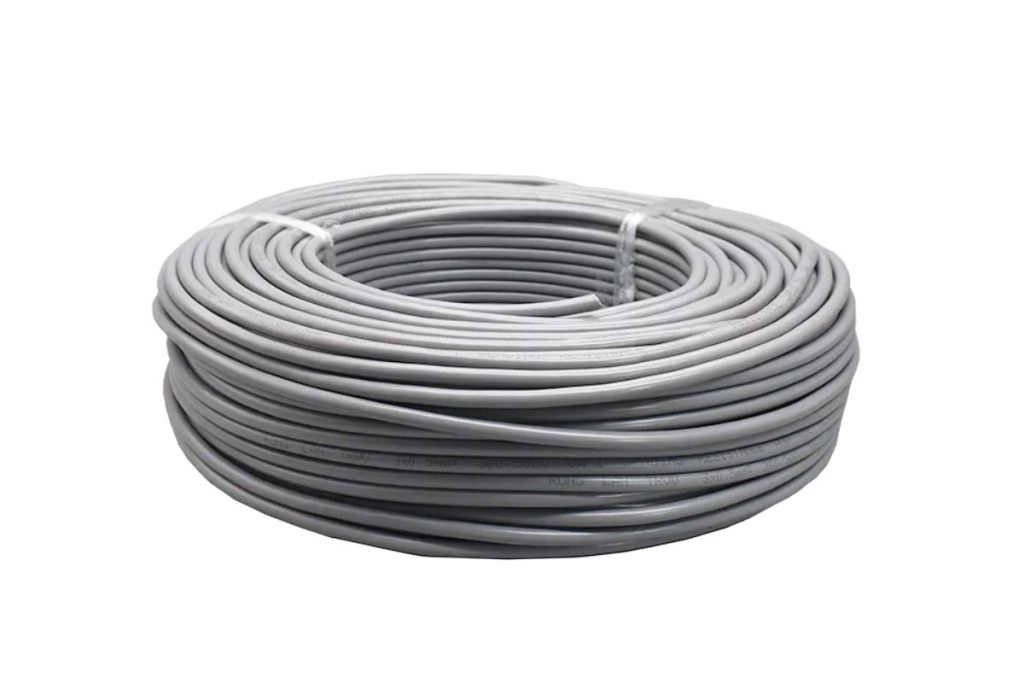
In addition to rubber, PVC compound insulated cables can also be vulcanized. PVC compound is prepared by mixing and kneading PVC as a base resin, together with plasticizers, stabilizers, inorganic fillers and other additives.
Aiming to improve the elasticity and abrasion resistance of PVC cable material, sulfur is added and vulcanized by pressurization and heating. Currently, Most vulcanized PVC cables are processed using flat vulcanizing units.
Los vulcanized PVC cables They are more common than vulcanized rubber cables due to their lower cost and suitability for certain applications..
Conclusion
Cable vulcanization plays an essential role in improving the properties of rubber and PVC insulation. This process increases resistance, durability and elasticity of the material, thus extending the life of the cables. The evolution of vulcanization methods has led to greater efficiency and productivity in cable production. As technology advances, It is possible to expect continuous improvements in the quality and performance of vulcanized cables, contributing to a safer and more reliable power supply in various applications.