Wire and cable manufacturing is a complex process that requires a variety of specialized equipment and tools to produce high-quality products.. All wire and cable processing begins with the conductor, and layers of insulation, appantallamiento, armor and jacket are processed layer by layer on the periphery of the conductor. The more complex the product structure, more cable manufacturing equipment is used.
Table of Contents
- Cable Manufacturing Equipment
- Dependency between Specialized Equipment and the Cable Manufacturing Process
- Continuous Innovation in Special Equipment
- Conclusion
Cable Manufacturing Equipment
Conductor Wire Drawing Machine
The first stage in cable manufacturing involves the transformation of copper wires or aluminum into finer wires and suitable for use in cables. The copper wire drawing machine is essential in this process, since it allows the reduction of the diameter of the copper or aluminum wire, guaranteeing the uniformity and quality required for the manufacture of cables.
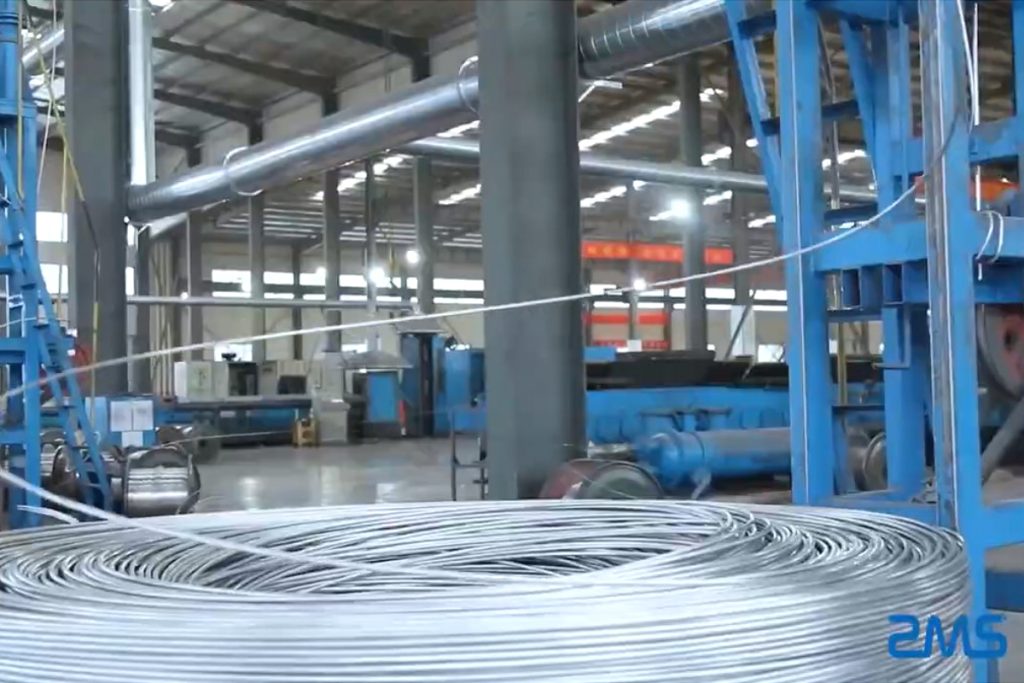
Braiding Machine
Braiding machines are essential for creating the internal structure of the cable. There are several types of braiding machines, like single and double, which are used to braid the internal conductors evenly. Choosing the right braiding machine depends on the specifications of the cable and its internal structure..
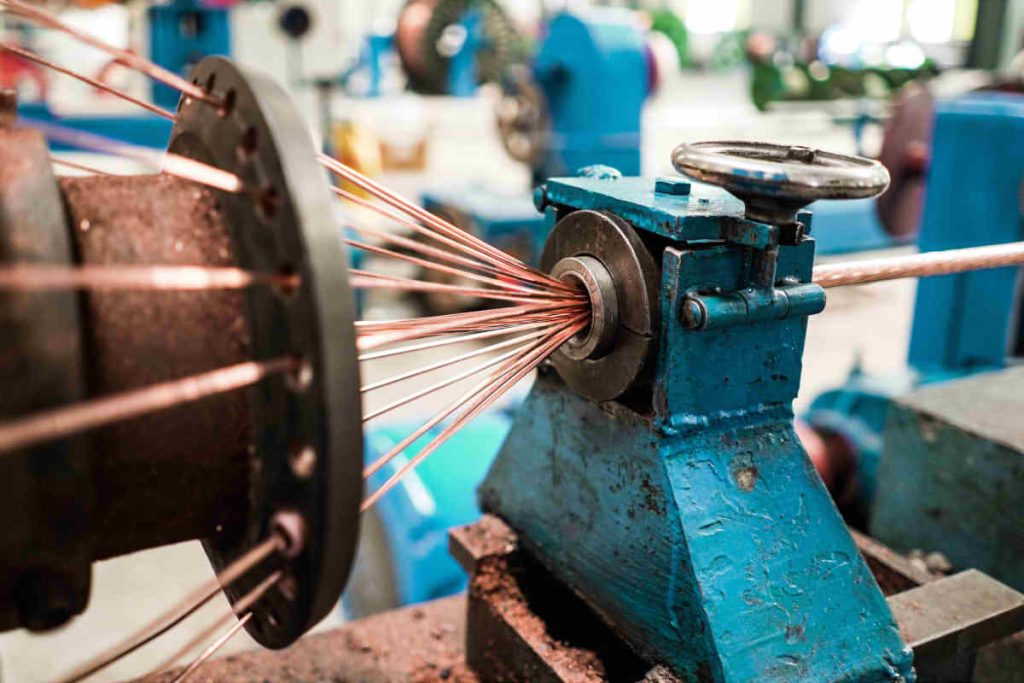
Extruder
The extruder is one of the central parts in the manufacture of cables. Its main function is to extrude high quality plastic material onto the insulated conductors. This creates an insulating layer that provides properties such as water resistance, to fire and abrasion, which is essential in the protection of the conductors and the durability of the cable.
Tape Wrapping Machine (Tape Wrapping Machine)
Tape wrapping machine is used to apply materials such as mica tape or aluminum-plastic tape to the outer layer of the cable.. This improves the insulation properties of the cable and protects it against mechanical damage., ensuring reliable performance in various conditions.
Steel Wire Truss Machine
In applications where additional strength is required, such as in high voltage cables or cables used in harsh environments, steel wire armor machine is used. This machine applies a reinforced layer of steel wire around the cable, providing increased tensile strength and protection against mechanical damage.
Weighing and Mixing Machine
For efficient cable sheath production, weighing and mixing machine is used. This machine allows for the precise mixing of different plastic materials and additives in specific proportions to create the proper composition for the cable sheath.. This optimizes product quality and reduces costs.
Sleeve Coating Machine
The sheath coating machine is essential for applying an outer layer of protection to the cable.. This sheath acts as an additional barrier that protects the cable from external damage and environmental factors., prolonging its useful life.
Injection Molding Machine
In some cases, injection molding machine is used to manufacture the cable sheath. This technique allows the creation of cable jackets with specific shapes and features for particular applications..
Zipper Machine (Zipper Machine)
The zipper machine is used to give the finishing touch to the manufactured cables, allowing it to be cut to specific lengths. This is especially important in the production of cables that must meet precise measurements for various applications..
Test Equipment
Cable quality and performance are crucial in many applications. Testing equipment plays an essential role in ensuring cables meet required quality standards. These devices can measure resistance, the tension, frequency and other parameters to verify the quality of the manufactured cable.
Dependency between Specialized Equipment and the Cable Manufacturing Process
Specialized cable production equipment has unique characteristics to adapt to the structure and performance requirements of product production.. The cable manufacturing process and the development of specialized equipment are closely related and promote each other. The new process requirements, promote the generation and development of new special equipment. At the same time, the development of new special equipment, and improve the promotion and application of new technologies. This is evident in several aspects of the cable manufacturing process..
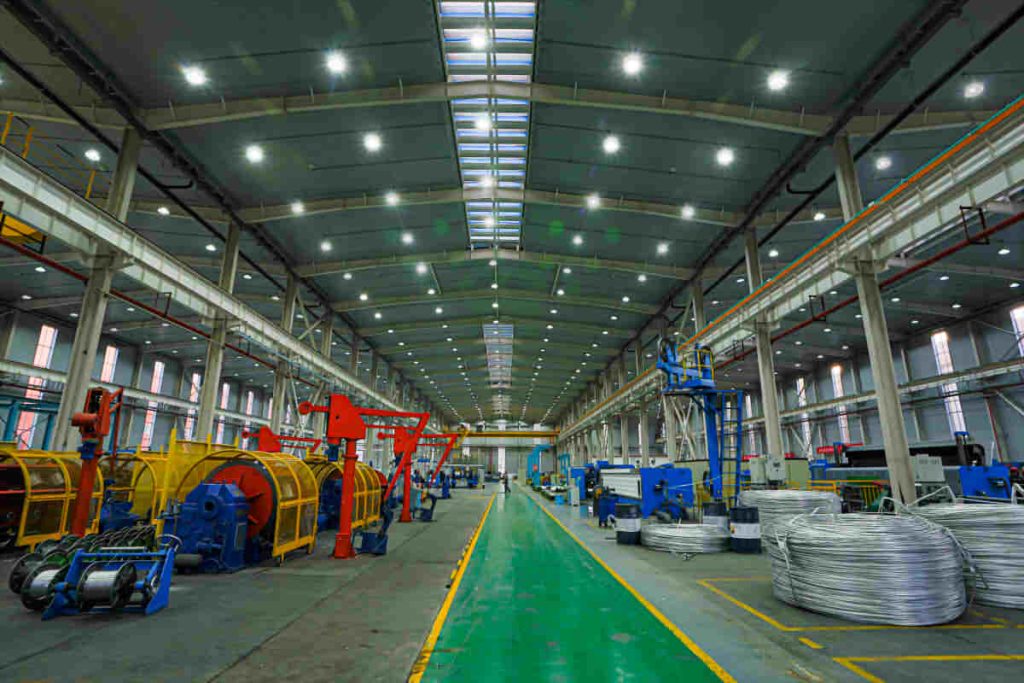
Stretching Lines, Annealing and Extrusion
Stretching lines, Annealing and extrusion are a perfect example of how the evolution of specialty equipment technology has boosted the cable manufacturing process.. These lines allow copper wires to be stretched to precise diameters and anneal them to improve their electrical conductivity. Besides, Plastic extrusion onto conductors has become essential to provide essential characteristics to cables, such as water and fire resistance. Thanks to these specialized lines, Cable production has become more efficient and the resulting cables are more reliable and secure.
Continuous Innovation in Special Equipment
Continuous innovation in specialized equipment is essential to keep up with changing industry demands. As new technologies and performance requirements emerge, Specialty equipment manufacturers respond by developing advanced solutions. This may include improvements in machine precision, process automation and the incorporation of digital technologies for real-time monitoring and production control.
For example, Modern extrusion machines are equipped with sophisticated control systems that allow the extrusion speed and temperature to be precisely adjusted., ensuring uniformity of insulation at all times. Besides, Production automation reduces dependence on labor and improves consistency in product quality.
Conclusion
In conclusion, Cable manufacturing is a highly specialized process that requires a wide range of specialized equipment to produce reliable and high quality cables. From copper wire drawing machine to cable tester, Each piece of equipment plays an essential role in the production of cables that are essential in our daily lives and in numerous industries.. These equipment not only improve the quality of the cables, but also contribute to the efficiency and security of the applications in which they are used.. Continued innovation in cable and equipment manufacturing technology ensures that we continue to see advances in cable quality and functionality in the future..