In recent years, The solar photovoltaic power generation industry has experienced rapid development, with an annual increase in the installed capacity of photovoltaic plants. Nevertheless, due to the lag in the research and promotion of specialized photovoltaic solar cables, during the construction and operation of these plants, Conventional cables are still used to connect the equipment of photovoltaic plants.
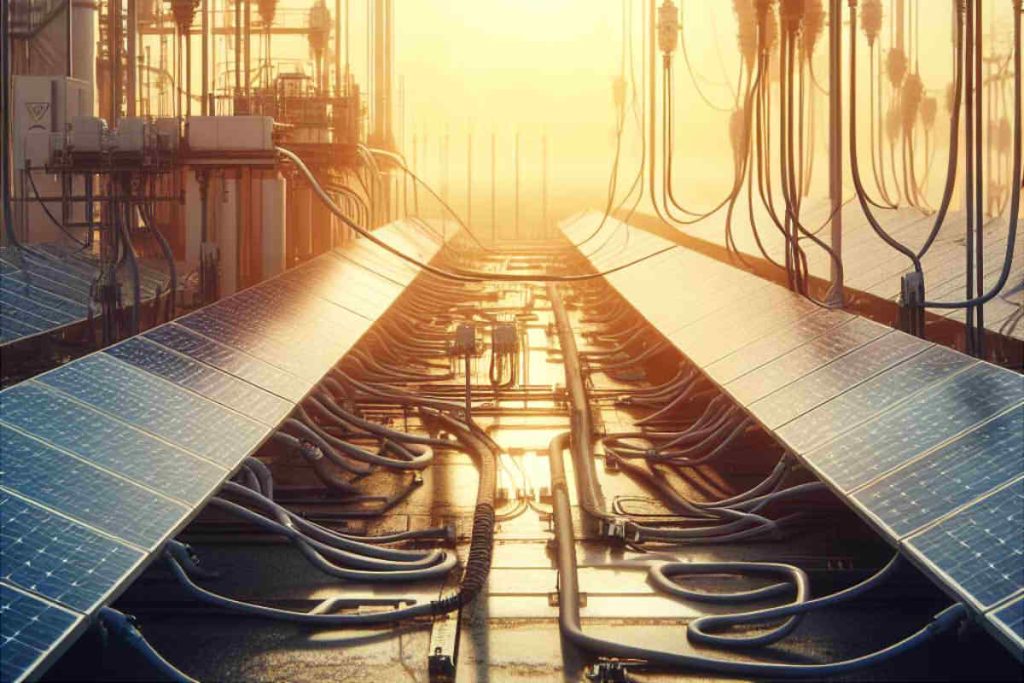
Table of Contents
- Specialized Photovoltaic Cables
- High or Low Temperature Resistance Requirements
- Requirements for Resistance to Humidity and Heat
- Requirements for Resistance to Sunlight and Ultraviolet Rays
- Acid Resistance Requirements, Alkalis and Salt Fog
- Ozone Resistance Requirements
- Conclusion
Specialized Photovoltaic Cables
Conventional cables do not meet the requirements for use because complex and changing environmental factors have not been taken into account in the operation and layout of solar photovoltaic power plants., which has led to frequent quality problems in these plants. Especially evident are the quality problems caused by the fact that the properties of the conventional electrical cables do not meet the requirements of the use environment of power stations.
Dedicated cables for photovoltaics are designed taking into account the complex and changing operating environment of solar photovoltaic power plants and can meet the layout and operation requirements of these plants.. The use of dedicated solar PV cables on the direct current side of solar PV power plants can effectively reduce the occurrence of quality problems..
High or Low Temperature Resistance Requirements
With the construction of photovoltaic solar power plants around the world, cables are required to have a wide range of temperature resistance. In some areas of the northern hemisphere, cables are required to be able to withstand extremely low temperatures, since in some regions temperatures can reach around -40 °C, and even lower.
By contrast, in some hot areas, the temperature at the surface can easily exceed +70 °C. Considering that the working temperature of the conductor is higher than the ambient temperature and generates heat when evaporating, at the same time, taking into account that in areas with poor ventilation in roofs and inefficient heat dissipation effects in structures, extreme temperatures could easily exceed +90 °C. This requires that the temperature of the cable material meets the plant's operating requirements in extreme weather conditions..
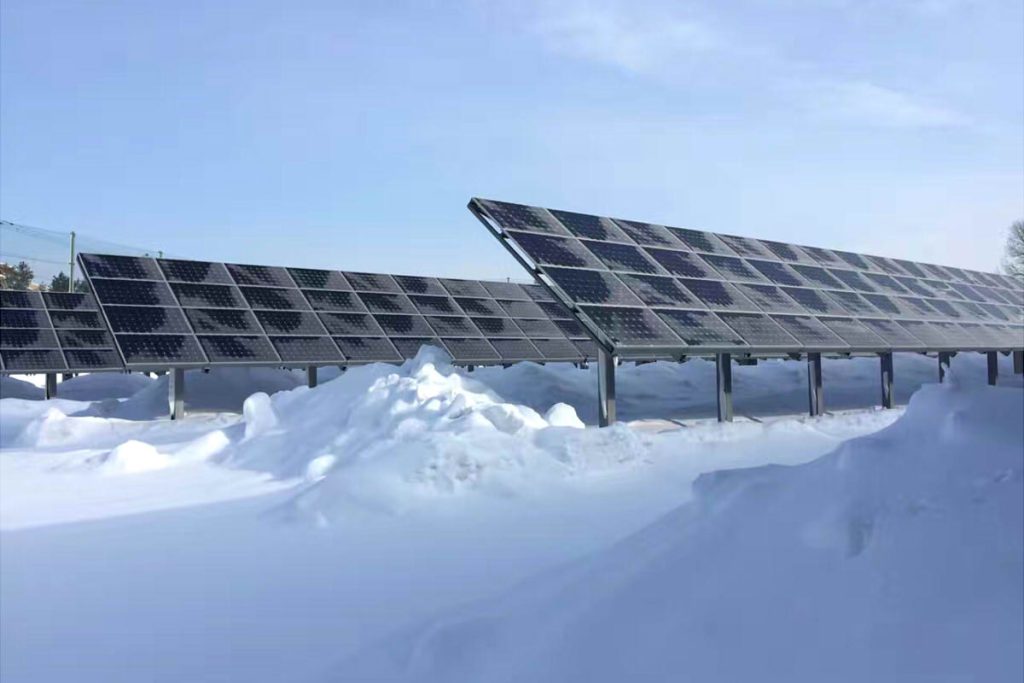
Los insulated cables have different properties temperature resistance depending on the materials used for insulation and cover. Next, A comparison between VV power cables is presented-0.6/1 yYJV-0.6/1, and the special ZMS cable for photovoltaics.
VV-0.6/1 Cable
The VV cable-0.6/1 generally uses polyvinyl chloride insulation (PVC) type J70 and PVC coating type H70. Both type J70 and type H70 have a maximum working temperature of 70 °C. When the ambient temperature or the working temperature of the conductor exceeds the 70 °C, J70 type insulation will soften and stick, which will result in decreased insulation performance and could lead to insulation failure, causing short circuits in the cable.
Besides, at temperatures above 70 °C, H70 coating will also soften and stick, losing its protective function. The impact brittle test of the H70 coating material is carried out at a temperature of -25 °C. Under these temperature conditions, passing the impact brittle test means the coating material is suitable for low temperature conditions. This also means that when the ambient temperature is lower than -25 °C, it is likely that the cable coating become brittle and crack, decreasing or losing its protective function.
YJV-0.6/1 Cable
YJV cable-0.6/1 uses cross-linked polyethylene insulation materials and HI-90 type PVC coating, both with a maximum working temperature of 90 °C. The impact brittle test of the HI-90 facing material is performed at a temperature of -20 °C. When the ambient temperature or the working temperature of the conductor exceeds the 90 °C, isolation will still experience decreased performance or failure issues. When the ambient temperature is lower than -20 °C, the protection function of the cable sheath will be reduced or lost.
Cable Solar Especial
Secondly, el ZMS cable solar especial uses cross-linked polyolefin insulation and coating materials 125 °C. As long as the ambient temperature and the maximum working temperature of the cable conductor do not exceed 125 °C, This type of cable will not experience problems of decrease or failure in insulation performance or reduction or loss of sheath protection function. Besides, The low temperature limit of the sheath material of this cable is -40 °C, which meets the requirements of low temperature environments in most regions.
Requirements for Resistance to Humidity and Heat
Frequent fluctuations in temperature and humidity have a direct impact on the aging of insulation and covering materials. This is especially relevant in areas with large daily and seasonal temperature variations., as well as in humid and rainy regions, where the impact on aging of insulation and covering materials is most pronounced. In practice, some solar photovoltaic power plants are located directly on the water, which implies that the cables must work normally in long-term humid environments.
Conventional cables do not take into account the effects of humidity and heat variation on the aging of materials. Instead, Specialized solar photovoltaic cables are designed considering these factors. Selected insulation and covering materials are tested to +90 °C y 85% humidity according to specified methods. After the tests, the reduction in tensile strength and elongation at break of the insulation and jacket does not exceed the 30%. Therefore, Qualified photovoltaic cables can meet the requirements of solar power plants in the face of temperature and humidity changes.
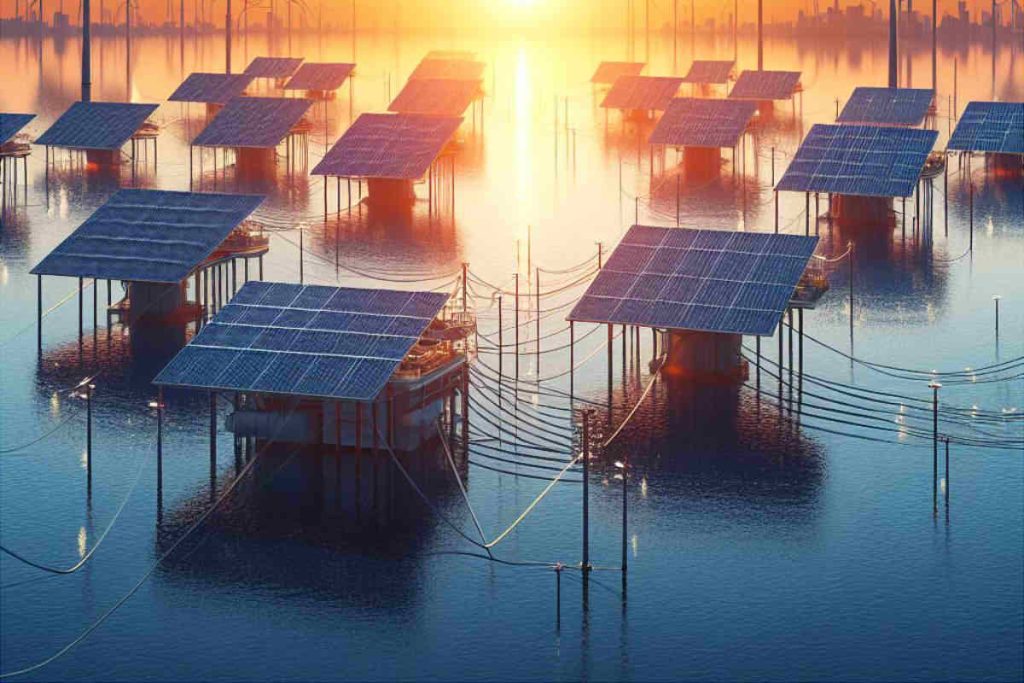
Requirements for Resistance to Sunlight and Ultraviolet Rays
Photovoltaic solar power plants are exposed to long periods of solar radiation intense, which includes a variety of solar radiation, especially ultraviolet rays that accelerate the aging of cable insulation and sheath. Many cables in photovoltaic plants are installed outdoors, from the solar modules to the junction box and even the cables to the inverters, and in most cases, these wires are directly exposed. This requires that the cables be able to resist sunlight radiation and ultraviolet rays., ensuring long-term normal operation under vertical radiation of sunlight and ultraviolet rays.
In areas such as deserts and sandy regions, cables used in solar photovoltaic power plants must consider resistance to sunlight and ultraviolet rays. According to the regulations of photovoltaic solar energy generation cable systems, These cables must pass artificial aging tests due to climatic conditions.
Therefore, Qualified photovoltaic cables can work normally for long periods under the radiation of sunlight and ultraviolet rays. Instead, conventional cables, Under these conditions, will see their aging accelerated in the insulation and the cover, which would result in a decrease or loss of insulation resistance and a decrease in jacket protection.
Acid Resistance Requirements, Alkalis and Salt Fog
Some solar photovoltaic power plants are located in special locations, such as near the sea or in marsh areas. In these areas, the concentration of salt in the air, especially in salt spray, is high. Besides, some photovoltaic solar power plants are located in former salt mines, where the salt content in the soil is high. In environmental conditions like these, The cables used must have a strong resistance to Saulty fog and be able to resist acidic and alkaline environments.
Solar PV cables designed for such environments use tinned copper conductors., which improves the oxidation and corrosion resistance of the conductor. Besides, Its cover can pass salt spray and alkali acid tests. Therefore, Qualified photovoltaic cables show strong resistance to salt spray and acid and alkali corrosion, while the technical standards applied to conventional electrical cables do not require resistance to salt spray or acid and alkaline environments..
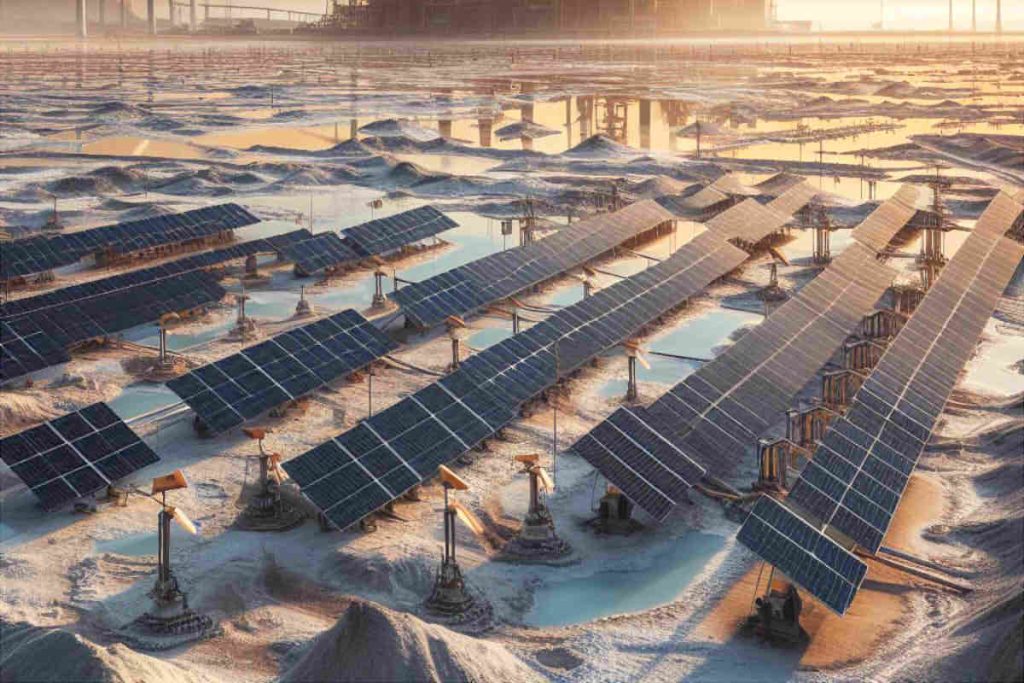
Ozone Resistance Requirements
Some areas where solar photovoltaic power plants are located have elevated ozone levels, and ozone can have a corrosive effect on cable sheaths, accelerating their aging and affecting their performance. Conventional cables do not take into account this corrosive effect of ozone on the cable sheath, while photovoltaic cables were designed taking this factor into account.
Los qualified cables photovoltaics must pass ozone resistance tests, which means that after 24 hours in an environment with an ozone concentration of 0.025-0.030%, the cover should not have cracks. Therefore, even in areas with elevated ozone levels, PV cables can work normally for long periods.
Conclusion
The mentioned characteristics that photovoltaic cables possess make them suitable for photovoltaic solar power plants in different environmental conditions., ensuring its safe long-term operation. By contrast, conventional cables have difficulty fulfilling this purpose.
Therefore, in solar power plant construction projects, especially on projects where the environment is particularly challenging, Choosing specialized solar PV cables instead of conventional cables effectively ensures the long-term and stable operation of the plant. This, at the same time, ensures sustainable and positive operational benefits of the plant over time.